Director, Operations
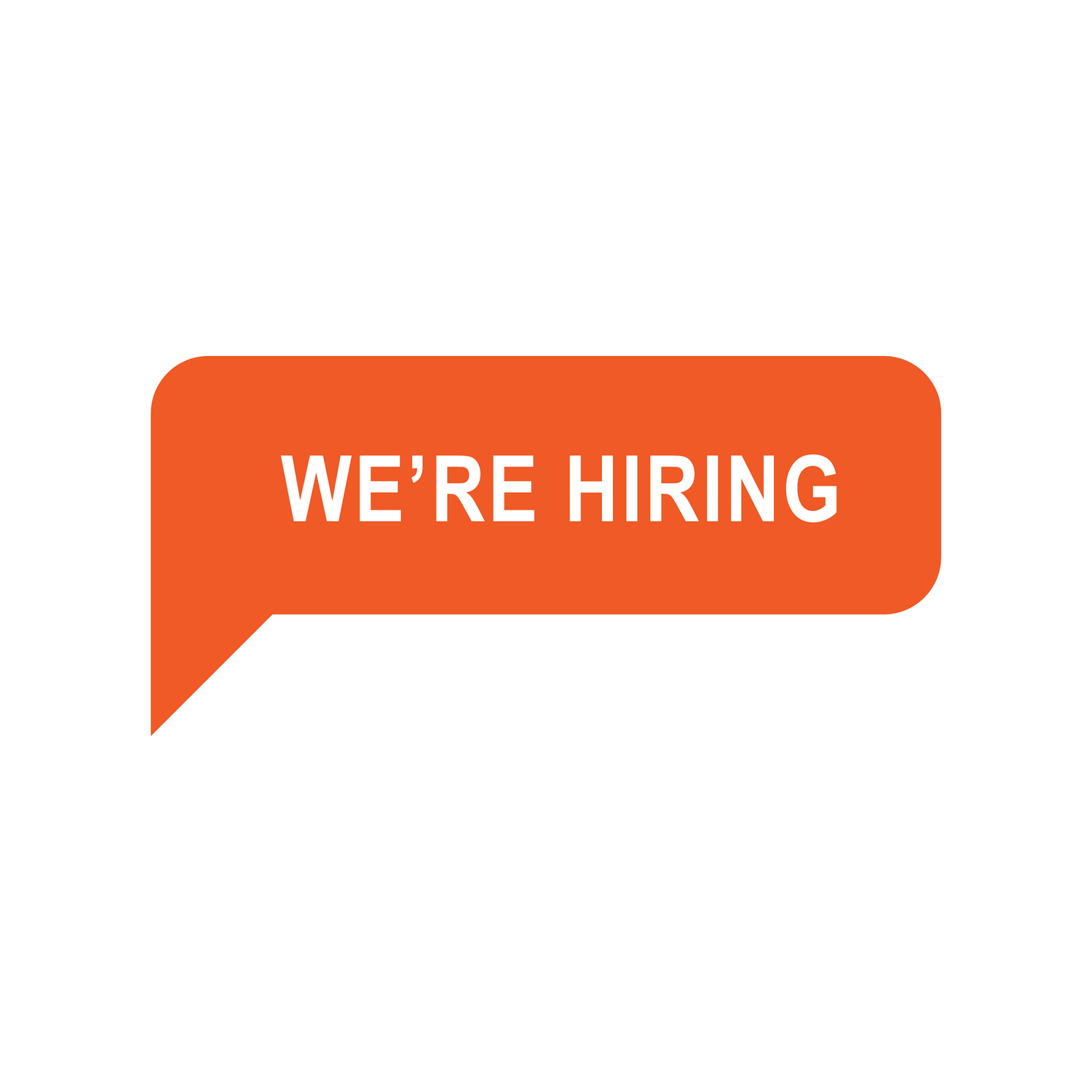
Ametek, Inc.
2024-05-06 19:02:25
Goleta,
California,
United States
Job type: fulltime
Job industry: Manufacturing Operations
Job description
Ametek, Inc.
SUMMARY:
Directs, coordinates, and exercises functional authority for planning, organization, control, integration, and completion of manufacturing operations. Responsible for the overall surveillance and success of assigned functions. Supervisory responsibility for Assembly & Test, Manufacturing Engineering, Production Control, Supply Chain Management, and Quality Assurance.
ESSENTIAL DUTIES include the following:
-
- Develop and implement policies & procedures that utilize LEAN Principles to support all aspects of Manufacturing Operations, including the sub-elements of Supply Chain Management, Quality Assurance, Assembly/Test, and Production Program Management.
- Plan and achieve company revenue and profit goals.
- Lead the preparation of the annual budget and strategic plan for Operations.
- Support company objectives for cost containment, including low-cost manufacturing/sourcing.
- Mentor and develop personnel responsible for Manufacturing Operations.
- Track and report KPI's to the Executive Management Team.
- Provide timely contract review to ensure that Company Objectives are achieved. This will include review and approval of Price Proposals and Customer Purchase Orders prior to acceptance.
- Ensure the effective use of the ERP system throughout the Manufacturing organization.
- Maintain a safe working environment and support compliance with regulatory requirements for environmental safety and health.
Education and Experience:Ed
-
- Proven record of success as a "hands-on" operations management leader with at least five years experience in a smilar role with history of progressively responsible career advancement.
- Experience in medium volume/high mix production environment, preferably in the military or aerospace industry.
- Bachelor's degree in an engineering discipline. Formal education and/or experience in Operations/Industrial Management.
- Relevant experiece utilizing Enterprise Resource Planning (ERP) systems. Oracle ERP experience a plus.
- 3-5 years experience in LEAN Principles preferred, LEAN/Six Sigma certification a plus.
- Experience in leading and developing personnel
Knowledge, Skills, Abilities:
-
- Strong oral and written communications skills. Ability to maintain focus and professionalism in a dynamic, fast-paced environment. Demonstrate effective communication skills with team members, company management, and customers.
- Requires knowledge of basic mathematics and analysis techniques as applied to manufacturing.
- Requires a high level of accuracy and attention to detail with ability to organize and synthesize data into meaningful, actionable information.
- Requires ability to effectively read and interpret documentation, i.e., drawings, specifications, contracts, agreements, government notices, company operating procedures, etc.
- Application of LEAN Manufacturing Principles to identify and eliminate waste from business processes in order to improve quality, cost and delivery.
- Knowledge of modern manufacturing processes used in the Aerospace Industries is preferred.
- Experience with Government Regulations and ISO-9000/AS-9100 Quality Management Systems.
- Soft Skills: Empathy, Honesty, Teamwork, Leadership, Coaching, Creativity and Problem Solving.
- Strong communication skills sufficient to effectively build a team and influence/motivate others.
- Strong Computer Skills.
License, Certification, or Preferred Qualifications:
-
- Technical background in aerospace design engineering, manufacturing, or repairs/maintenance.
- Business degree or certification.
- LEAN/Six-Sigma certification.
Physical Demands & Work Environment:
-
- Requires the ability to access all areas of the facility.
- Infrequent need to lift light loads (up to 25 lbs.).
Tools Used:
- Personal computer and software (ERP, MS Office Suite).
SUMMARY:
Directs, coordinates, and exercises functional authority for planning, organization, control, integration, and completion of manufacturing operations. Responsible for the overall surveillance and success of assigned functions. Supervisory responsibility for Assembly & Test, Manufacturing Engineering, Production Control, Supply Chain Management, and Quality Assurance.
ESSENTIAL DUTIES include the following:
-
- Develop and implement policies & procedures that utilize LEAN Principles to support all aspects of Manufacturing Operations, including the sub-elements of Supply Chain Management, Quality Assurance, Assembly/Test, and Production Program Management.
- Plan and achieve company revenue and profit goals.
- Lead the preparation of the annual budget and strategic plan for Operations.
- Support company objectives for cost containment, including low-cost manufacturing/sourcing.
- Mentor and develop personnel responsible for Manufacturing Operations.
- Track and report KPI's to the Executive Management Team.
- Provide timely contract review to ensure that Company Objectives are achieved. This will include review and approval of Price Proposals and Customer Purchase Orders prior to acceptance.
- Ensure the effective use of the ERP system throughout the Manufacturing organization.
- Maintain a safe working environment and support compliance with regulatory requirements for environmental safety and health.
Education and Experience:
-
- Proven record of success as a "hands-on" operations management leader with at least five years experience in a smilar role with history of progressively responsible career advancement.
- Experience in medium volume/high mix production environment, preferably in the military or aerospace industry.
- Bachelor's degree in an engineering discipline. Formal education and/or experience in Operations/Industrial Management.
- Relevant experiece utilizing Enterprise Resource Planning (ERP) systems. Oracle ERP experience a plus.
- 3-5 years experience in LEAN Principles preferred, LEAN/Six Sigma certification a plus.
- Experience in leading and developing personnel
Knowledge, Skills, Abilities:
-
- Strong oral and written communications skills. Ability to maintain focus and professionalism in a dynamic, fast-paced environment. Demonstrate effective communication skills with team members, company management, and customers.
- Requires knowledge of basic mathematics and analysis techniques as applied to manufacturing.
- Requires a high level of accuracy and attention to detail with ability to organize and synthesize data into meaningful, actionable information.
- Requires ability to effectively read and interpret documentation, i.e., drawings, specifications, contracts, agreements, government notices, company operating procedures, etc.
- Application of LEAN Manufacturing Principles to identify and eliminate waste from business processes in order to improve quality, cost and delivery.
- Knowledge of modern manufacturing processes used in the Aerospace Industries is preferred.
- Experience with Government Regulations and ISO-9000/AS-9100 Quality Management Systems.
- Soft Skills: Empathy, Honesty, Teamwork, Leadership, Coaching, Creativity and Problem Solving.
- Strong communication skills sufficient to effectively build a team and influence/motivate others.
- Strong Computer Skills.
License, Certification, or Preferred Qualifications:
-
- Technical background in aerospace design engineering, manufacturing, or repairs/maintenance.
- Business degree or certification.
- LEAN/Six-Sigma certification.
Physical Demands & Work Environment:
-
- Requires the ability to access all areas of the facility.
- Infrequent need to lift light loads (up to 25 lbs.).
Tools Used:
- Personal computer and software (ERP, MS Office Suite).