Sr. Reliability Engineer
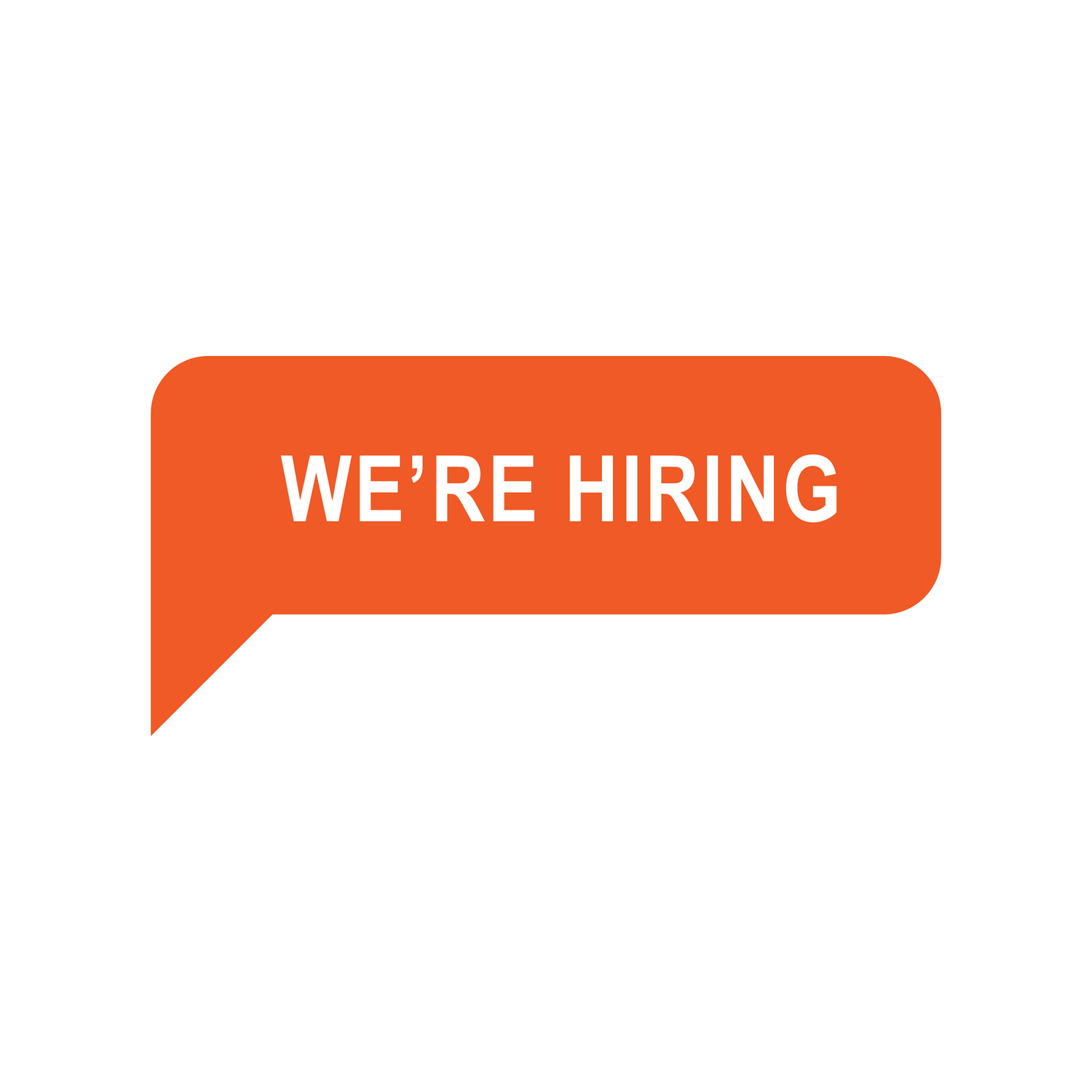
CSL
2024-11-05 05:41:29
Kankakee,
Illinois,
United States
Job type: fulltime
Job industry: Trades & Services
Job description
This position is responsible for the equipment reliability and maintenance strategy of utility and manufacturing equipment through continuous monitoring and analyzing of equipment operational performance and initiating preventive actions needed for improvement (Reliability-Centered Maintenance). This position works collaboratively with the global Maintenance & Utilities Excellence organization to ensure alignment with the global reliability strategy.
Role that this position reports to: Sr Manager, Reliability Engineering
Responsibilities:
Technical Lead for Equipment Reliability:
Creation of maintenance strategies for new, critical plants (utilities and manufacturing) as a basis for the creation of maintenance plans.
Serve as the reliability leader within the organization, mentoring and coaching less experienced engineers and technicians on best practices in equipment reliability and mechanical integrity.
Lead reliability improvement teams and collaborate with other departments (e.g., Operations, Maintenance, Engineering) to address equipment issues and improve overall plant reliability.
Promote a culture of reliability and continuous improvement through proactive leadership, problem-solving, and cross-departmental collaboration.
Develop, implement, and maintain comprehensive maintenance strategies and mechanical integrity (MI) plans for plant equipment, including pressure vessels, piping, and rotating equipment, especially with focus on new, critical plants.
Continuously improve maintenance programs (PMs), Bill of Materials (BOMs), and spare parts inventories to ensure regulatory compliance.
Collaborate with engineering teams on equipment classification, SAP functional location (FLOC) structure (FLOC), asset information population, and acquisition of equipment manuals.
Reliability Analytics:
Use reliability engineering tools like data analysis techniques (statistical process control, reliability modeling and prediction, fault tree analysis, Six Sigma (6σ) methodology, machine learning algorithms etc.), root cause analysis (RCA), Failure Modes and Effects Analysis (FMEA) and failure reporting, analysis, and corrective action system (FRACAS ) in accordance with global standards to analyze maintenance and integrity data trends.
Develop predictive maintenance models to forecast equipment failures and implement proactive maintenance actions, minimizing unplanned downtime and extending equipment lifespan.
Identify and implement opportunities for reliability and mechanical integrity improvement to enhance equipment uptime and performance.
Develop KPI dashboards to visualize reliability data and performance metrics, enabling better decision-making and communication of reliability improvements to stakeholders to showcase improvements in maintenance and mechanical integrity practices.
Measure and report reliability and mechanical integrity performance metrics such as Mean Time Between Failures (MTBF), Mean Time to Repair (MTTR), equipment downtime, and maintenance costs.
Mechanical Integrity and Inspection Programs:
Oversee mechanical integrity programs to ensure the safe and reliable operation of pressure vessels, piping systems, and rotating equipment.
Implement and manage risk-based inspection (RBI) programs to ensure compliance with industry standards and regulatory requirements (API, ASME, OSHA).
Ensure that all equipment meets mechanical integrity standards through regular inspections and the application of non-destructive testing (NDT) methods.
Management of CMMS Data Integrity & Reliability-Centered Maintenance (RCM):
Ensure CMMS data integrity to support preventive, predictive, and condition-based maintenance processes, including mechanical integrity requirements.
Oversee maintenance planning processes and the evaluation of new predictive technologies in closed collaboration with the global Maintenance & Utilities Excellence organization to be aligned with the global strategy.
Lead the application of predictive maintenance (PdM) technologies and non-destructive testing (NDT) methods to minimize downtime and ensure the structural integrity of critical assets.
Asset Health monitoring for Predictive Maintenance:
Ensure close and collaborated cooperation in this area with the global Maintenance & Utilities Excellence organization to be aligned with the global strategy.
Implement and manage condition-based monitoring programs using IoT and sensor-based technologies to monitor the health and mechanical integrity of critical assets.
Utilize real-time sensor data to detect early signs of equipment degradation and initiate proactive actions.
Act as the Subject Matter Expert (SME) for internal and regulatory audits concerning equipment reliability, mechanical integrity, and maintenance.
Ensure compliance with mechanical integrity standards such as API 510, 570, 653, ASME, and OSHA.
Continuously enhance knowledge in biopharmaceutical industry best practices, mechanical integrity, and problem-solving techniques.
Ensure adherence to CSL Behring's Safety Program, complying with OSHA and health and safety mandates, particularly in areas related to mechanical integrity.
Complete additional duties assigned by senior management to support reliability, mechanical integrity, and plant operations.
Qualifications:
Bachelor degree in Mechanical, Electrical or Industrial Engineering preferred or M.S. degree in an Engineering related field
5-7 years' experience with relevant experience in maintenance engineering, mechanical integrity, or reliability engineering, preferably in the pharmaceutical or manufacturing industry.
Certified in Data Analysis (Preferred but not required).
Certified Maintenance & Reliability Professional (CMRP) (Preferred but not required).
Certified Reliability Engineer (CRE) (Preferred but not required).
Certified in Mechanical Integrity (API 510, 570, or 653 certification preferred).
Demonstrated knowledge of reliability engineering concepts such as Total Productive Maintenance (TPM), Reliability-Centered Maintenance (RCM), and Failure Mode and Effect Analysis (FMEA).
Hands-on experience with failure analysis methodologies (RCFA) and process improvement principles such as Lean and/or Six Sigma.
Strong proficiency in computerized maintenance management systems (CMMS).
Familiarity with tools like Power BI, QlickSense, for creating interactive visualizations and dashboards (plus).
Familiarity with cloud platforms like SAP 4/HANA.
Experience with AI/ML project deployment pipelines (plus).
In-depth knowledge of Good Manufacturing Practices (GMPs), FDA standards, and other regulatory guidance.
Strong verbal, technical writing, and interpersonal skills.
Ability to work cross-functionally, collaborate with various teams, and solve complex technical problems.
Different qualifications or responsibilities may apply based on local legal and/or educational requirements. Refer to local job documentation where applicable.
CSL employees that work at least 30 hours per week are eligible for benefits effective day 1. We are committed to the wellbeing of our employees and their loved ones. CSL offers resources and benefits, from health care to financial protection, so you can focus on doing work that matters. Our benefits are designed to support the needs of our employees at every stage of their life. Whether you are considering starting a family, need help paying for emergency back up care or summer camp, looking for mental health resources, planning for your financial future, or supporting your favorite charity with a matching contribution, CSL has many benefits to help achieve your goals.
Please take the time to review our benefits site to see what's available to you as a CSL employee.
About CSL BehringCSL Behring is a global leader in developing and delivering high-quality medicines that treat people with rare and serious diseases. Our treatments offer promise for people in more than 100 countries living with conditions in the immunology, hematology, cardiovascular and metabolic, respiratory, and transplant therapeutic areas. Learn more about CSL Behring .
We want CSL to reflect the world around usAs a global organization with employees in 35+ countries, CSL embraces diversity and inclusion. Learn more about Diversity & Inclusion at CSL.
Do work that matters at CSL Behring!