Sr Industrial Engineer
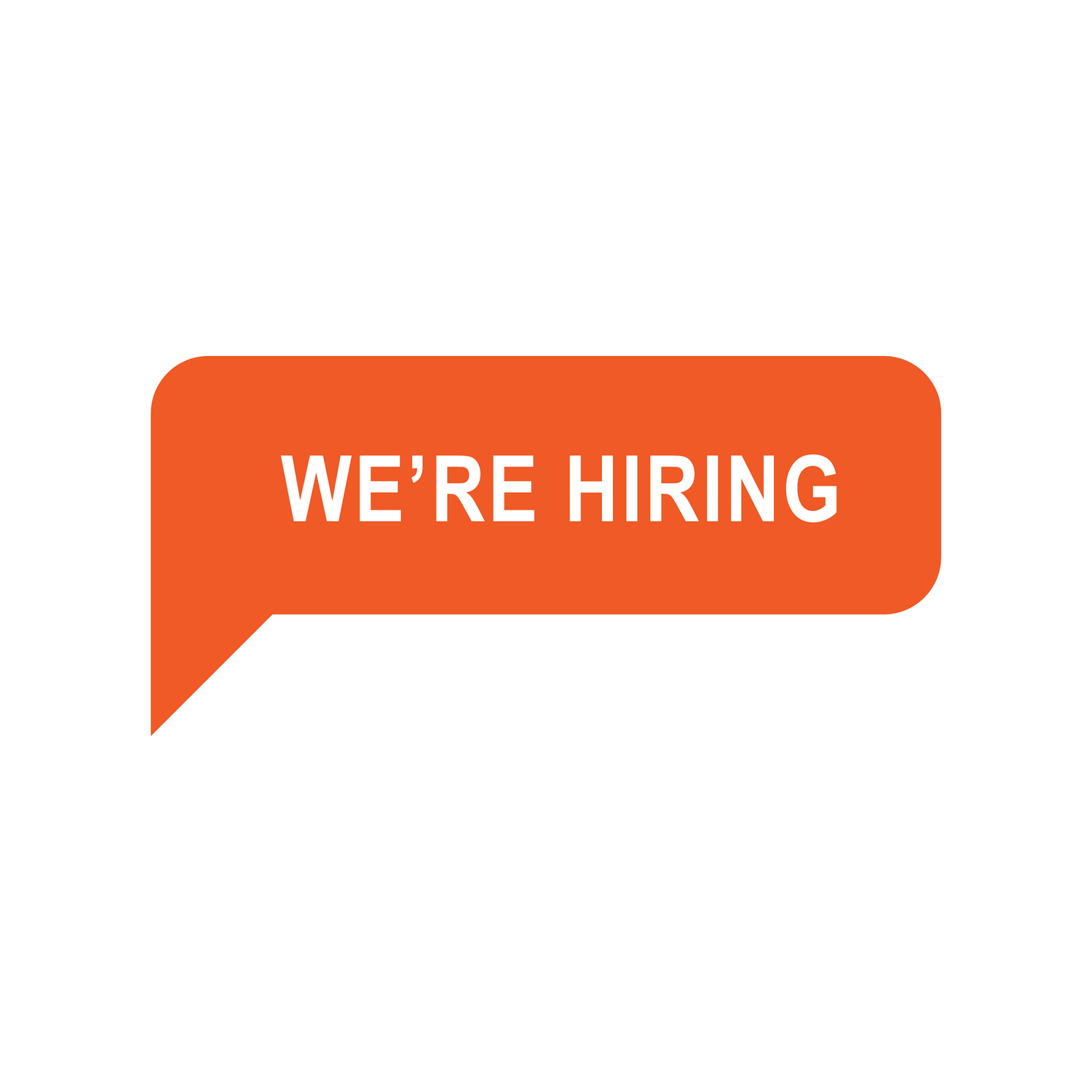
Continental Tire The Americas, LLC
2024-11-08 13:42:36
Clinton,
Mississippi,
United States
Job type: all
Job industry: Engineering
Job description
Continental Tire The Americas, LLC is one of the largest automotive manufacturers in the world and a leader in automated driving. Through our pioneering technologies and services, were changing the future of mobility to make it more safe, smart, and sustainable. Our Clinton, MS location is seeking a Sr Industrial Engineer to join our team. Are you ready to shape the future with us? THE POSITION Sr Industrial Engineer, Continental Tire The Americas, LLC, Clinton, MS: Design, integrate or improve tire manufacturing systems. Carry out time studies, maintain standard time data, analyze losses data / OEE (Overall Equipment Effectiveness) / TEEP (Total Effective Equipment Performance). Implement standard times with production and employee representatives/union and ensure data quality for industrial engineering systems. Analyze available machine capacity. Calculate required production manning based on production volume targets. Collect and prepare data for capacity debottlenecking, strategic projects. Actively participate in business team meetings, follow-up on efficiency and losses development, improvement of OEE/TEEP, performance goal setting and ensure the CBS (Continental Business System) approach is being applied within the cross functional business team. Follow up on correct application of standards with production and support development of standard operating procedures. Conduct improvement workshops on the shop floor with production and any other stakeholders within the area of responsibility. Define machine layout for production area and micro workplace layout to ensure high efficiency and ergonomics for operation. Define layout or material storage areas in production to facilitate efficient material handling and ensure FEFO (First Expired, First Out) principle. Carry out material flow and work process analysis, lead time analysis and job evaluation studies. Develop future capacity, layout and material flow concepts for the production area. Facilitate improvement and growth projects and workshops to improve the standards (including workplace design, design of work organization, processes, layout, material flow design). Define machine and process parameters to create requirement catalogues together with production and engineering. Carry out benchmarking studies comparing process key figures with other plants and identify possibilities for process improvement based on the analyzed data in cooperation with production and engineering. Calculate potential savings of identified measures in the production area. Carry out feasibility studies of improvement measures. Conduct value stream exercises to identify areas requiring improvements. Full time employment, Monday Friday, 40 hours per week. MINIMUM REQUIREMENTS: Bachelors degree in Engineering (any), Statistics or a related field and 2 years of related work experience. Of the required experience, must have 2 years of experience in all of the following: Tire manufacturing experience, including experience with process engineering, maintenance, industrial engineering or quality; Preparing standard operating procedures for operators with focus on process efficiency and product quality; Utilizing Structured Problem Solving (SPS) techniques, including A3; Tracking and measuring process performance related to efficiency, capability and yield in each stage of the tire manufacturing process; Monitoring and analyzing tire manufacturing plant shop floor output evaluation (including production and process data) to ensure optimum levels of production and identify any bottlenecks; Monitoring and analyzing losses data to determinate areas of improvements within the tire manufacturing process, working with cross functional teams to develop and implement process improvements; Increasing the efficiency and quality of the tire manufacturing process by implementing process improvements and managing lean manufacturing tools, including TPM (total productive maintenance), 5S methodology or SMED (Single-Minute Exchange of Die); and Coordinating the work of a cross functional group, including quality technicians, operators and maintenance, on at least two tire manufacturing projects at the same time. International travel required up to 5%. Domestic travel required up to 5%. To Apply, email resume to with Job ID 242424 in subject line. In compliance with applicable laws, Continental Tire The Americas, LLC is committed to employing only those who are authorized to work in the US. Applicants must be legally authorized to work in the U.S. as Continental Tire The Americas, LLC will not engage in immigration sponsorship for this position. All qualified applicants will receive consideration for employment without regard to race, color, religion, sex, sexual orientation, gender identity, national origin, disability, or status as a protected veteran.