Please scroll down, To apply
Environmental, Health and Safety Coordinator from Metals Manufacturing Environment
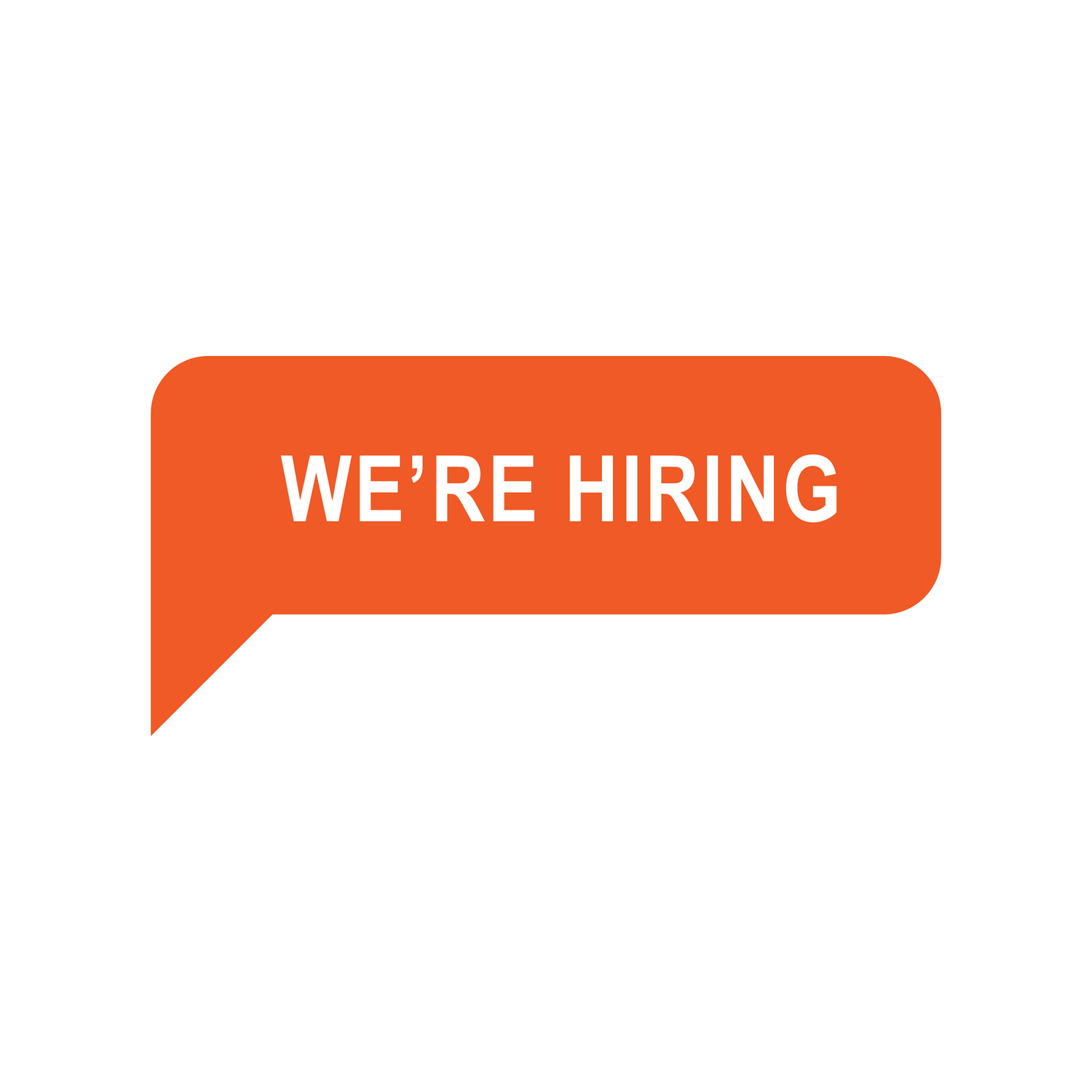
Macpower Digital Assets Edge Private Limited (MDA Edge)
2024-09-20 10:49:11
Eupora,
Mississippi,
United States
Job type: fulltime
Job industry: Manufacturing Operations
Job description
WHAT WE OFFER YOU:
- Salary: $60,000 to $85,000 depending on experience
- Benefits effective 30 days from date of hire.
- Medical, Dental and Vision, HSA, FSA.
- 401k Matching, Life Insurance, STD/LTD.
- 100% covered tuition reimbursement (including books & reasonable expenses).
- Wellness Program/Lifestyle Rewards /Employee Assistance Program (EAP).
- Paid Time Off & Holidays.
- Career Arching: We allow for a great depth & breadth of knowledge in which you can wear many hats and be exposed to several opportunities.
- Our client is looking for an enthusiastic, ambitious team member to join our EHS team. This person must embrace change, be self-motivated, and inspire others inside and outside the department.
- The individual should be able to communicate directly and openly with all levels in our organization.
- There will be many opportunities for the successful candidate to engage their innovative and creative problem-solving skills to help move the department to the next level.
- It is a must that the EHS Coordinator has a high degree of personal integrity in dealing with customers, superiors, subordinates, and co-workers and will represent us in a professional manner.
- The successful candidate will live both in the big picture as well as in the details, desire to make an impact, and work well in a team and individually.
- As an Environmental, Health and Safety Coordinator you will ensure coordination of the environmental, health and safety activities.
- An ideal candidate will have at least 2 year experience in EHS in a metals manufacturing environment, or similar.
- Experience with OSHA regulatory requirements and regulations and experience with Safety training, and compliance reporting.
Safety:
- Strong knowledge of OSHA regulatory requirements & ensures implementation for compliance.
- Investigates the root causes of accidents & prepares reports with findings & corrective actions.
- Ensure active Safety Teams are in place.
- Develops Safety Training Calendar for the Mill annually.
- Coordinates & conducts all Safety training to ensure compliance.
- Conducts Safety & Environmental Orientation for new hires.
- Manages the Safety Portion of the Corporate EHS Management System for the Salisbury mill.
- Manages & oversees all safety incident compliance & reporting, ensures proper internal reporting, and records all information on the OSHA 300, 301 and 301A as needed.
- Leads safety culture & initiatives with front line leadership, admin staff and acts as a resource for the groups.
- Evaluates organization's exposure to safety hazards through inspections and monitoring of the facility.
- Ensures an active JSA program is in place.
- Participates in Rapid Improvement Events throughout the year to provide safety support & insight.
- Meets with State & Federal OSHA inspectors should they visit the site.
- Manages the Emergency Action Plan and drills.
- Leads others to find creative safety solutions within complex manufacturing processes.
- May lead functional teams or projects with moderate resource requirements.
- Ensures continuous improvement & evolution of EHS processes & performance within the facility.
- Support the dissemination of the annual EHS plans and various training programs.
- Provide comprehensive case management for injured employees.
- Communicate EHS concepts clearly and concisely to all levels of employees both verbally & in written form.
- Conduct periodic inspections to ensure compliance with company standards and develop corrective actions as required.
- Leads the Safety Coaches program to help with safety ownership on the production floor.
- Manages the Environmental Portion of the Corporate EHS Management System
- Oversees waste handling activities conducted by Waste Operations personnel and via 3rd party services.
- Coordinates all waste disposal and ensures proper recordkeeping.
- Ensures environmental compliance with all applicable environmental permits for the mill.
- Completes all environmental reports and inspections as legally required.
- Deep Involvement in environmental related projects.
- Ensures awareness around all capital projects within the mill and its impacts on environmental regulations.
- Ensures mill compliance with all EPA/state and local environmental regulations.
- Develops an annual environmental training calendar and ensures all environmental training is completed.
- Evaluates the mill's risks around environmental exposure.
- Oversees the Wastewater Department to ensure water is being treated properly.
- Oversees Acid Pickle Area to ensure EHS activities are being maintained and waste activities are reduced.
- Participates in 3rd Party environmental audits conducted by outside attorneys.
- Conduct periodic inspections to ensure environmental compliance with government & company standards & develop corrective actions as required.
- Participates in production & staff meetings to ensure EHS related activities are properly communicated.
- Participates in kaizen & lean activities to ensure EHS related activities are properly communicated & updated.
- May support activities with capital project(s) as needed.
- May assist with other department roles, activities or job responsibilities as needed.
- Own and role model Plymouth Tube values and behaviors by embracing and participating in an operating culture that promotes involvement, communication, mutual trust & respect, expectations and accountability, and a passion for excellence.
- Understands, applies, and advocates all Company Environmental and Safety policies, procedures and standards.
- Understands, applies, and advocates all Company Quality Standards.
- Attends all prerequisite training as required by management.
- May complete off site waste audits.
Education and/or Experience:
- Bachelor in environmental, Health and Safety, preferred-preferred but not required.
- 2+ years' experience in a manufacturing environment in an EHS role or a combination of comparable years and experience considered.
- Comprehensive knowledge of the field's concepts and principles.
- Windows operating systems & programs
- Microsoft Office Suite
- Ability to use calipers.
- Can speak and communicate effectively with technical and non-technical team members.
- Can correctly interpret documents such as written instructions, spreadsheets, drawings, lists and manuals.
COMPETENCIES:
- Regulatory Compliance : A strong understanding of relevant environmental, health, and safety regulations and standards, such as OSHA, EPA, and relevant local regulations.
- Risk Assessment : The ability to identify and assess potential hazards and risks within the manufacturing processes, machinery, and work environment.
- Safety Management Systems : Proficiency in implementing and maintaining safety management systems that include policies, procedures, and protocols to prevent accidents and injuries.
- Environmental Management : Knowledge of environmental management practices, including waste management, air and water quality monitoring, and pollution prevention.
- Incident Investigation : Skill in conducting thorough investigations into workplace accidents, incidents, and near misses to determine root causes and develop corrective actions.
- Emergency Response Planning : Ability to develop and implement emergency response plans and procedures to address potential crises such as fires, chemical spills, and other accidents.
- Training and Education : Proficiency in designing and delivering effective training programs to educate employees about safety protocols, environmental practices, and emergency procedures.
- Personal Protective Equipment (PPE) : Knowledge of appropriate PPE selection, usage, and maintenance to ensure worker safety.
- Hazard Communication : Ability to manage and communicate information about hazardous materials and chemicals in the workplace, including proper labeling and safety data sheets (SDS).
- Industrial Hygiene : Understanding of industrial hygiene principles, including monitoring, and controlling exposure to harmful substances such as dust, fumes, and noise.
- Ergonomics : Knowledge of ergonomic principles to design workspaces and processes that minimize strain and injury to employees.
- Audit and Inspection : Proficiency in conducting regular inspections and audits to identify potential EHS deficiencies and ensure compliance with regulations and company policies.
- Data Analysis : Skill in analyzing EHS-related data . click apply for full job details
<!– job description page –>