Reliability Engineer III
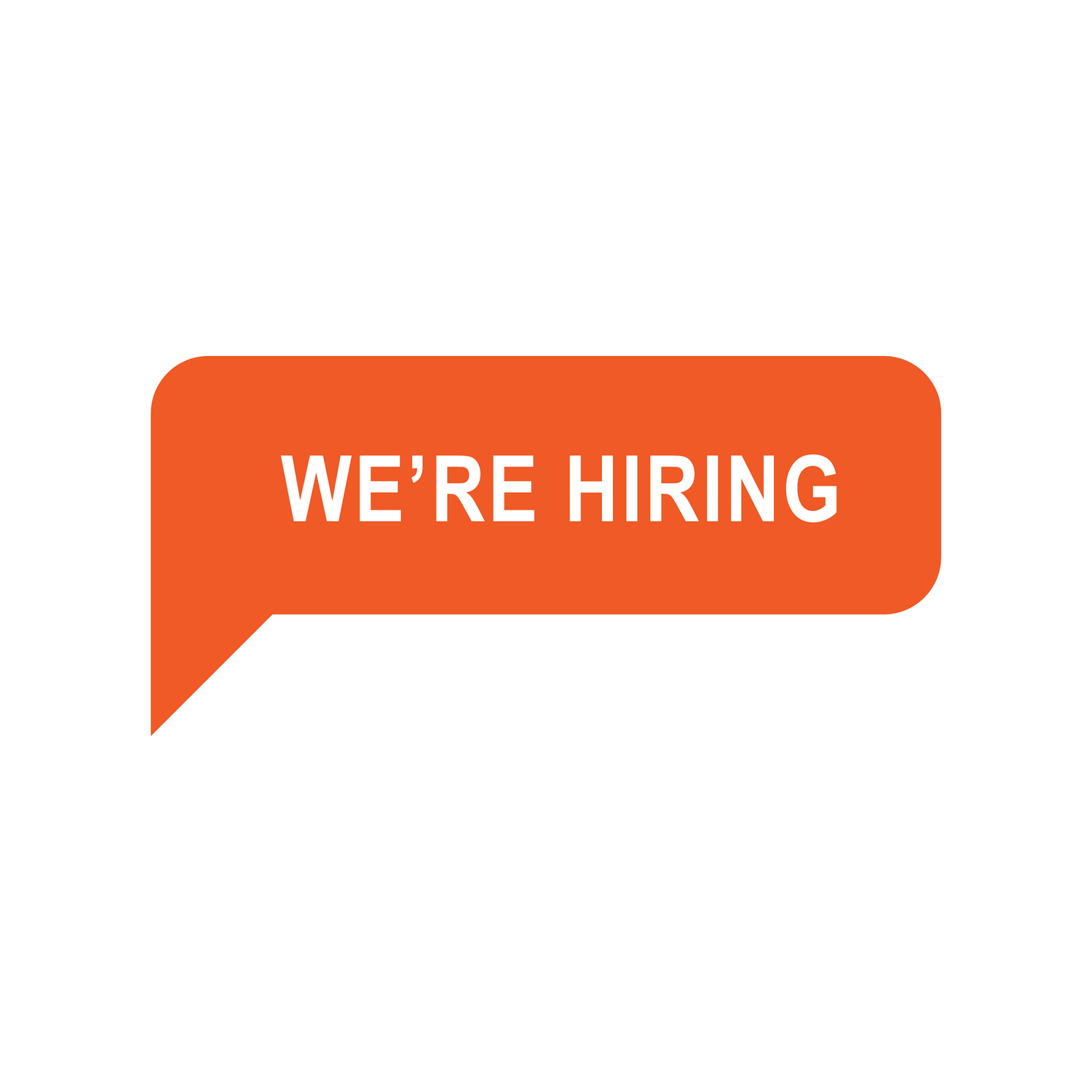
NES Fircroft 120000.00 US Dollar . USD Per annum
2024-11-05 05:41:55
Blair,
Nebraska,
United States
Job type: fulltime
Job industry: Engineering
Job description
Start Date: ASAP
Length of Assignment: Direct Hire
Full Site Address: Blair, NE 68008
Cost Center: 368092
Pay Rate: $120,000/year - 130,000/year + up to 13% potential bonus
Relocation package available if needed.
Company Overview:
Client is an advanced materials company offering a broad portfolio of renewably-sourced polymers and chemicals to the packaging, polymers, fibers, and chemicals markets. With performance and economics that compete with oil-based plastics and fibers, naturally advanced Ingeoâ polymers are valued for their unique functional properties and are used in consumer products from coffee capsules and electronics to diapers and wipes. and in larger applications like 3D printing materials.
Client is jointly owned by Cargill and Thailand's largest, and ASEAN's leading, integrated petrochemical and refining company, PTT Global Chemical.
Diversity and Nondiscrimination Statement:
Client brings together employees with a wide variety of backgrounds, skills, and cultures. Combining such a wealth of talent and resources creates the diverse and dynamic teams that consistently drive our results. We provide equal opportunities to all employees without regard to personal characteristics, such as race, color, gender, national origin, age, religion, disability, veteran status, marital status, sexual orientation, or other characteristics protected by law.
Job Family Overview:
Within the Manufacturing function, the Engineering family is accountable for identifying opportunities and creating value for Client and customers through multiple engineering disciplines. Work includes assessing gaps, identifying solutions and measurements, performing capital project development and implementation, determining and supporting best practices to the organization and customers, and providing engineering training and support.
POSITION PURPOSE:
The Reliability Engineer 3 is responsible for driving the improvement of plant reliability and champion defect elimination efforts through engineered solutions. This position will apply knowledge and experience to ensure continuous improvement to optimize the company's physical assets and maintenance and reliability processes and strategies. The Reliability Engineer will support the continued implementation and leadership of the Reliability Excellence process.
The Reliability Engineer is responsible for supporting the Technology / Plant Operations team by developing functional strategies, setting new standards and developing and implementing new processes that have a short to mid-term impact on the organization and achieve the mission, vision and goals of the organization.
KEY ACCOUNTABILITIES:
Reliability Excellence (50%)
- Leads development and implementation of Maintenance and Reliability (M&R) strategies to achieve business and customer objectives
- Identifies, investigates, develops and implements required actions, utilizing engineering practices to prevent & eliminate defects in critical plant assets
- Develops M&R management systems to achieve compliance and continuously improve performance
- Collaborates with Plant leadership, operations, maintenance staff, and contractors as required to develop and implement appropriate responsive programs for asset management
- Seen as a functional subject matter expert for reliability for the company
- Coordinates and acts as a resource for M&R training for facility personnel
- Provides reliability input to Capital Project activities
- Directs Asset Capability (AC) and Asset Mechanical Reliability (AMR) business objectives for their site
- Facilitation and implementation of the RCI process to include application of the cause and effect methodology in all areas where reliability opportunities are identified and where the RCI triggers are met
- Maintains a reliability model that identifies the unit operations, equipment, process, etc. that identifies the value of opportunities for improvement
- Evaluates and quantifies the impact projects such as equipment reconfigurations, design changes, equipment quality, etc. will have on ability to meet customer needs
- Evaluates effectiveness of individual aspects of the PPM program by showing quantitatively the impact of failures and PPM through the use of reliability engineering principles/tools such as RCM analysis, FMEA, etc.
- Analyzes asset utilization and cost data to develop and prioritize a list of reliability opportunities
- Evaluates/validates the impact of corrective actions that impact availability and/or reliability and leverages solutions across plants/site if appropriate
- Ensures Management of Change Process is followed/implemented for reliability changes/improvements
- Participates in front end loading activities such as: Process Simplification, Value Engineering, Maintenance Strategy, Reliability Modeling, etc.
- Participates in company assessments study and efforts to implement corrective action to maintain or improve plant conditions
- Develops effective, diverse leaders who are well trained, engaged, and focused on operational excellence for today and for the future. This focuses on the following: hiring and retaining diverse talent, training and development, performance management, engagement, balance between leadership and technical expertise, and a culture focused on operational excellence
- Support company policies and procedures as a member of management for all employees; presents a professional image as a representative of the company
- Creates an environment focused on continuous learning and improvement, fostering close-knit collaboration sparked by the energy of a startup
- Establishes and maintains effective professional working relationships with co-workers and every level of management
- Operates safely within Client policies, procedures and governmental regulations and fully participates in and champions Client Environmental, Health & Safety (EH&S) Programs
- Ensures the EH&S Programs are being followed and provides a safe working environment to our employees and customers
- Accountable for building a strong safety culture and actively pursues it on a daily basis; identifies unsafe behaviors and conditions and intervenes to mitigate incidents
Qualifications:
Education and Experience Required:
- Bachelor's degree from four-year college or university in mechanical, electrical, chemical, or other related engineering/technical field
- 7+ years of Maintenance or Reliability experience in a chemical manufacturing facility
- Specializes in at least one discipline (Reliability Best practices, or Rotating, Fixed, Electrical, or Instrumentation)
- Demonstrated ability to solve complex technical problems using formal techniques to evaluate systems, equipment, and processes
- Experience using Reliability Centered Maintenance techniques, cause analysis, and predictive maintenance technologies such as vibration analysis, infrared, acoustic emissions, tribology, etc.
- Proficient in various computer programs
- Certified Maintenance and Reliability Professional (CMRP)
- Supply Chain certification (Six Sigma, Lean, APICS, etc); knowledge and experience in Lean manufacturing and kaizen principles
- Training in Weibull, RCI, FMEA, RCM, RBI, Modeling, etc. facilitation would be helpful.
- Project Management experience and knowledge
- Thorough understanding of ensuring the safety of manufacturing areas and work practices in accordance with the site Environmental, Health & Safety programs
- General knowledge of production management with the ability to develop understanding of plant processes and operational needs
- Strong knowledge of process engineering fundamentals and unit operations
- Certification with the International Society of Automation is beneficialCompany Overview:
Client is an advanced materials company offering a broad portfolio of renewably-sourced polymers and chemicals to the packaging, polymers, fibers, and chemicals markets. With performance and economics that compete with oil-based plastics and fibers, naturally advanced Ingeoâ polymers are valued for their unique functional properties and are used in consumer products from coffee capsules and electronics to diapers and wipes. and in larger applications like 3D printing materials.
Client is jointly owned by Cargill and Thailand's largest, and ASEAN's leading, integrated petrochemical and refining company, PTT Global Chemical.
Diversity and Nondiscrimination Statement:
Client brings together employees with a wide variety of backgrounds, skills, and cultures. Combining such a wealth of talent and resources creates the diverse and dynamic teams that consistently drive our results. We provide equal opportunities to all employees without regard to personal characteristics, such as race, color, gender, national origin, age, religion, disability, veteran status, marital status, sexual orientation, or other characteristics protected by law.
Job Family Overview:
Within the Manufacturing function, the Engineering family is accountable for identifying opportunities and creating value for Client and customers through multiple engineering disciplines. Work includes assessing gaps, identifying solutions and measurements . click apply for full job details