Quality Supervisor 3rd Shift
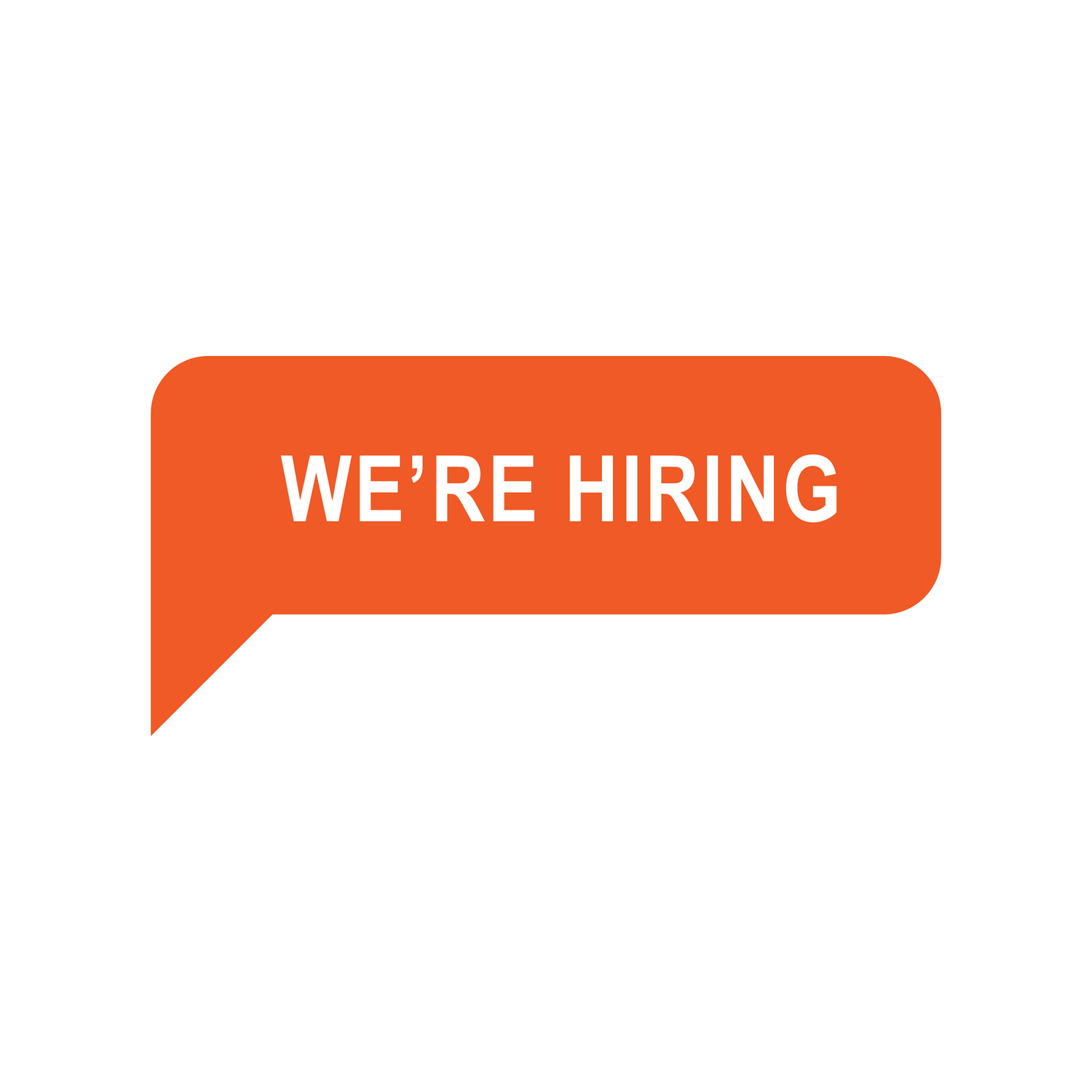
MasterBrand Cabinets LLC
2024-11-07 16:43:27
Lexington,
North Carolina,
United States
Job type: fulltime
Job industry: Other
Job description
Job Description
The Quality Supervisor is responsible for overseeing and managing the day-to-day operations of the quality team to ensure that products and processes meet the company's quality standards, customer requirements, and regulatory guidelines. This role involves supervising daily quality operations, conducting audits, training and developing staff, troubleshooting quality issues to ensure that production and operational processes are carried out efficiently and effectively, and driving continuous improvements to enhance product quality, minimize defects, and optimize processes. The Quality Supervisor works closely with production, engineering, materials, and other departments to foster a culture of quality throughout the organization.
Key Responsibilities:
Quality Oversight: Supervise, guide, and mentor a team of quality specialists, technicians, and support staff ensuring adherence to quality standards, procedures, and regulatory requirements throughout production and assembly processes.
Inspection & Testing: Oversee the inspection and testing of products, ensuring compliance with internal quality standards and specifications. Lead investigations and corrective actions for any identified non-conformances.
Process Improvement: Identify and lead initiatives to enhance product quality, reduce defects, and improve overall manufacturing efficiency. Identify areas for process optimization, implement corrective actions, and lead continuous improvement initiatives. Collaborate with other departments to enhance product quality, reduce waste, and improve efficiency.
Documentation & Reporting: Maintain and review detailed records of inspections, test results, and quality-related data. Prepare reports on product quality, trends, and performance, presenting findings to management and relevant stakeholders.
Training & Development: Train team members on quality processes, standards, regulatory requirements, and best practices. Foster continuous improvement through ongoing learning and skills development.
Root Cause Analysis: Investigate and resolve quality issues or non-conformances, conducting root cause analysis and implementing corrective actions.
Collaboration & Communication: Work cross-functionally with production, engineering, materials, and management to ensure the highest quality standards are maintained. Provide guidance on quality-related issues and support in problem-solving efforts.
Compliance & Standards: Ensure that the team is adhering to all company policies, industry regulations, and quality standards.
Audit Support: Conduct regular internal quality audits and assist with external audits. Ensure that quality control processes are being followed and that all findings are documented, reported, and addressed.
Customer Complaints & Non-Conformance Management: Manage the investigation of customer complaints related to quality issues and work to resolve them promptly. Ensure non-conformances are addressed through root cause analysis and corrective action plans.
Supplier Focus: Manage material non-conformances by working with suppliers to disposition material and prevent reoccurrences.