Building Maintenance Worker
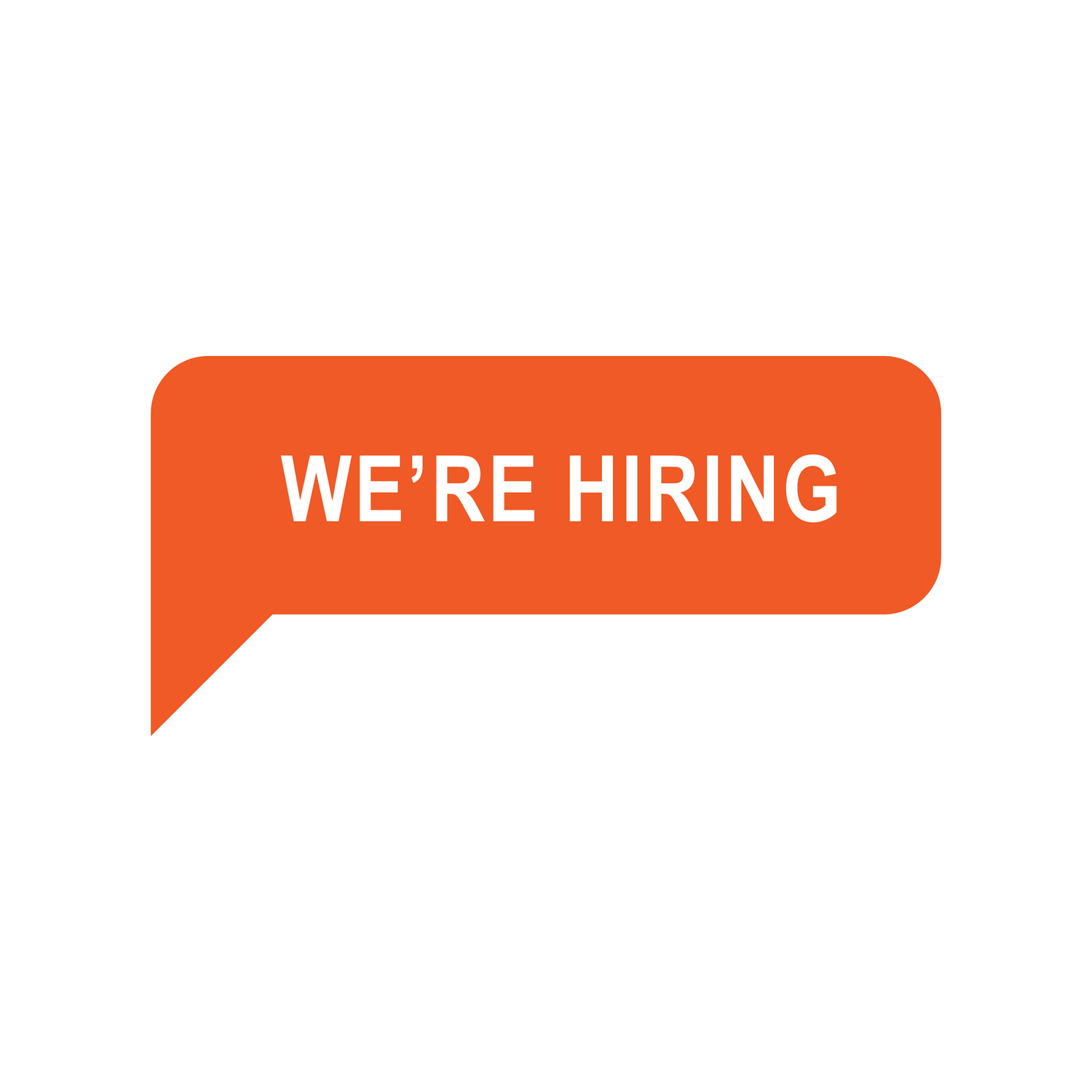
RAD Engineered Wood Products
2024-11-14 11:46:55
Nescopeck,
Pennsylvania,
United States
Job type: fulltime
Job industry: Construction
Job description
Description:
Summary
The Maintenance Manager is responsible for ensuring the facilities, layout, and machinery run to their maximum efficiency and output. This position is responsible for providing direction and guidance to all maintenance technicians for machine breakdown, preventative maintenance and ongoing projects as well as safety and general maintenance throughout the facility. An ongoing partnership with various levels of management and external vendors is essential to effectively manage both workload and personnel within the department. This position will train and develop employees to maintain compliance and build competent team members with various and dynamic skillsets. It is essential to drive a preventative and ongoing plan that adheres to environmental, health, and safety requirements.
Major Duties And Responsibilities
- Leads the site maintenance function by providing proactive and reactive response to maintenance services on all operational equipment and facilities infrastructure.
- Increases site productivity by identifying and fulfilling maintenance needs, knowledge-gaps, and areas for continuous improvement.
- Establish technical best practices and standard work and procedures to drive consistency and improve overall department performance.
- Recommend and execute projects and improvement programs while practicing frugality and time management.
- Actively leads and participates in Gemba walks to conduct real-time observation identifying hazards and waste in the manufacturing process while taking in consideration safety, material handling and storage, and inventory of resources.
- Manages, coaches, and develops a high performing team that meets agreed upon goals and objectives. Provides team with ongoing constructive feedback for professional growth within organization.
- Develops a planned preventative maintenance plan (PPM) schedule to ensure all preventative maintenance is carried out timely and develops a plan for any missed or new maintenance activities.
- Organizes and manages the schedules of the maintenance personnel as well as their timecard and time off.
- Maintains inventory of all parts and stocks all wearable parts and essential spares for equipment throughout the facility as well as sourcing and purchasing parts, negotiating prices and maintaining relationships with outside vendors.
- Track all downtime including root causing analysis and making recommendations and implementing processes and procedures to mitigate future downtime issues.
- Partners with operators to gather feedback, identify larger organization-wide projects or initiatives leading to improved processes.
- Stay current and up to date on any changes that may effect the supply and demand of needed products and materials and advise management of the impact.
- Maintains regular and reliable attendance
- Other duties as assigned
Physical Demands & Working Conditions
- Visual acuity, with or without corrective lenses
- Ability to hear speech and/or alarms through noise on the production floor
- Standing, reaching with hands and arms, and using hands and fingers to manipulate instrument or equipment controls, computer keyboard, office equipment, objects and tools
- Movement from one work location to another
- Standing often for extended periods of time
- Safely lifting objects up to 50 lbs.
- Temperature within manufacturing plant may vary between 60- 90 degrees, and can occasionally exceed 90 degrees
- Exposure to intermittent or constant sounds generated by equipment
- Exposure to fumes, noxious odors and dust
- Handling of toxic or caustic chemicals
- Proximity to moving parts
Education & Experience
- Associate's degree or equivalent required preferably within the Engineering field
- 10 years' experience in manufacturing/production preference within a maintenance setting
- 5 years' experience in a managerial role
- Electrical and mechanical aptitude required
- Demonstrated supervisory skills with proven experience in leading a maintenance team
Knowledge, Skills, & Abilities
- Demonstrates aptitude for electrical and mechanics
- Thorough understanding of applicable safety and quality processes and procedures
- Intimate operating knowledge of processing equipment within the facility
- Ability to identify process failures when they happen and coach the team through problem solving
- Ability to interpret and execute various technical procedures in verbal, written, mathematical or diagrammatical form
- Ability to work in a team environment and motivate others to meet demands established by the schedule
- Proficient knowledge of OSHA safety practices
- Possesses excellent verbal and written communication skills
- Possesses excellent organizational skills and attention to detail
- Ability to adapt to changes and continuous improvement initiatives
- Demonstrates a high level of integrity
As with all jobs at our company, a consistently positive, cooperative, self-motivated, courteous and professional attitude is essential to successful performance. Other statements included in this job description represent typical elements and criteria required; they are not intended to be all-inclusive and are subject to modification by our company and its designees.
PI446bd2202b7d-8455