Manufacturing Lean Ranger
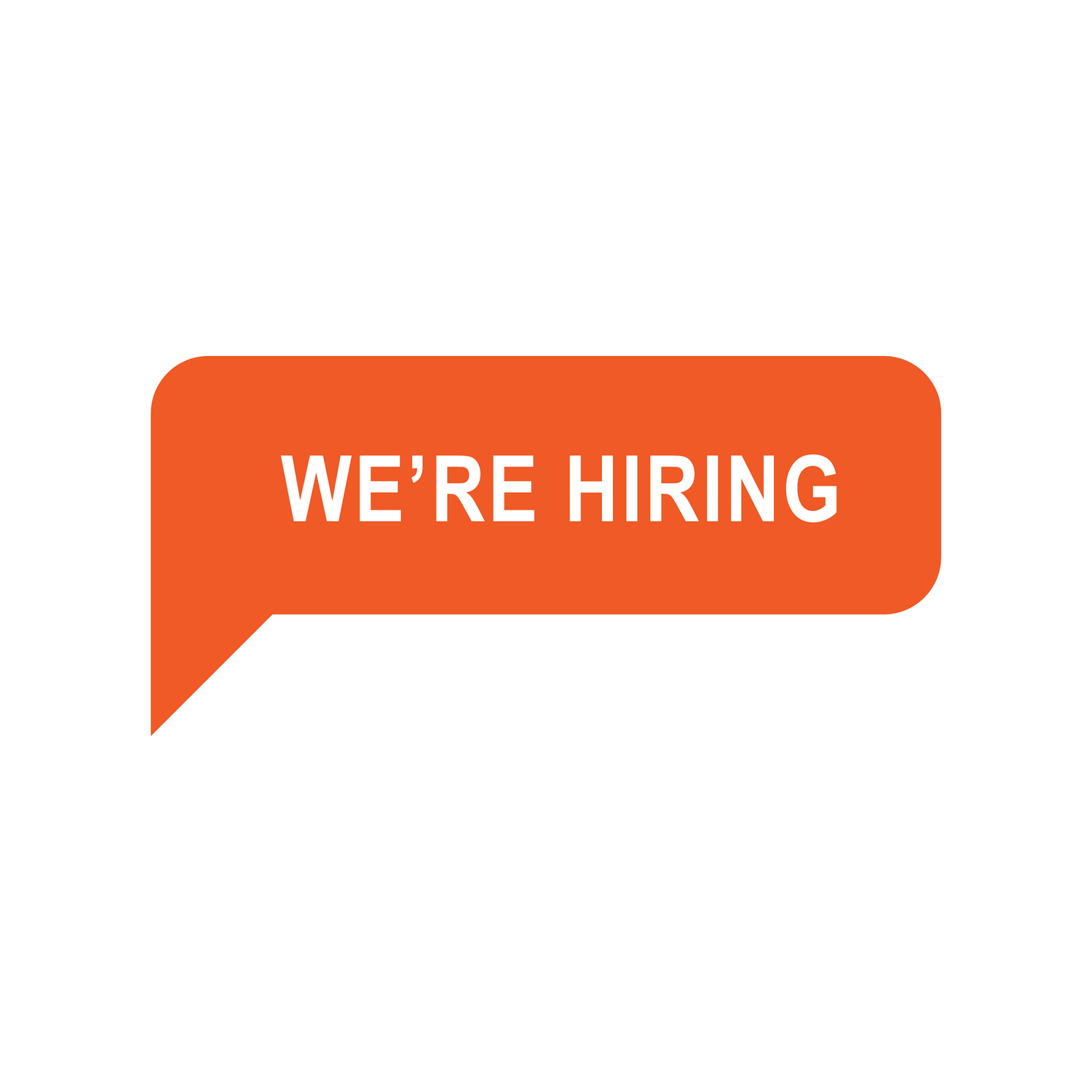
Wilo EMU USA LLC
2024-11-06 22:43:27
Collierville,
Tennessee,
United States
Job type: fulltime
Job industry: Manufacturing Operations
Job description
Description:
Wilo USA LLC is a subsidiary of Wilo SE, which is headquartered in Dortmund, Germany. Wilo is one of the leading manufacturers of pumps and pump systems for heating, cooling, and air-conditioning solutions, water supply, and sewage and drainage. Wilo USA acquired Weil Pump and Scot Pump in 2017, American-Marsh Pumps in 2019, QuantumFlo in October 2021, and HydroServ in May 2023.
We offer exceptional benefits: Health, Dental, Vision, Life and Critical Illness Insurance, Employee Assistance Program, Health Savings Account, 401(k) and match, Tuition Reimbursement, PTO 19 days, 10 holidays, and 6 sick days.
Job Summary
A successful Manufacturing Lean Ranger is knowledgeable in process improvement, lean management, and safety standards, with solid leadership and communication skills. They will be adept at driving change, enhancing workplace organization, and sustaining improvements across departments.
Primary Job Duties
- Lead the implementation and sustainment of 6S (Sort, Set in order, Shine, Standardize, Sustain, and Safety) principles across the facility.
- Conduct regular audits and inspections to ensure compliance with 6S standards, identify areas for improvement, and address deficiencies.
- Train and mentor staff on the 6S methodology, building a solid understanding of 6S principles at all organizational levels.
- Develop and execute continuous improvement projects to improve operational efficiency, reduce waste, and promote a safer workplace.
- Collaborate with cross-functional teams to standardize processes and maintain best practices throughout the organization.
- Analyze operational workflows and processes to identify inefficiencies and implement improvement initiatives.
- Monitor and measure the success of 6S initiatives by tracking key metrics and reporting progress to senior management.
- Work closely with the safety team to ensure that 6S practices align with all safety protocols and regulatory requirements, including OSHA compliance.
- Act as the subject matter expert on Lean Manufacturing, Six Sigma, and other process improvement techniques, driving a culture of continuous improvement.
- Lead 6S training programs for new employees and refreshers for existing staff, ensuring consistent application of 6S principles.
- Foster a positive working environment by encouraging employee engagement and feedback, helping to sustain long-term improvement.
Locations: Collierville, TN
Direct Reports: 0
Travel Requirements: 0
Pay Range: Commensurate with experience.
Shift/hours: Normal business hours are 6 am to 2:45 pm; overtime is available.
Relocation: This position is not eligible for relocation assistance.
Visa Sponsorship: This position is not eligible for visa sponsorship. Applicants must be currently authorized to work in the United States.
PM22
Requirements:Education and Experience:
- Bachelor's degree in Industrial Engineering, Operations Management, Business, or a related field. Equivalent experience may be considered.
- Lean Six Sigma Green Belt or Black Belt certification is strongly preferred.
- Proven experience implementing and managing 6S or similar continuous improvement methodologies in manufacturing or operations environments.
- Strong knowledge of Lean Manufacturing, Six Sigma, Kaizen, and other process improvement tools.
- Project management experience with a track record of successfully leading cross-functional teams and improvement projects.
- Excellent analytical and problem-solving skills with the ability to identify root causes and implement effective solutions.
- Exceptional leadership and communication skills, with experience in training, coaching, and mentoring teams.
- Strong attention to detail and the ability to maintain high standards of safety and organization.
- Familiarity with OSHA safety standards and other relevant regulatory requirements.
- Proficiency in using data analysis tools (such as Excel, Minitab, or other statistical software) to monitor performance metrics and progress.
- Experience with ERP/MRP systems to support operational changes is a plus.
Physical Demands and Work Environment
The physical demands described here are representative of those that an employee must meet to successfully perform the essential functions of this position. Reasonable accommodations may be made to enable individuals with disabilities to perform the functions.
- Regularly required to sit or stand, reach, bend, and move about the facility.
- Office: Standard office equipment; work usually performed in an office setting free from any disagreeable elements.
PI431f671f7d6e-9568