PGD Plant Technician - McCommas - Dallas, TX
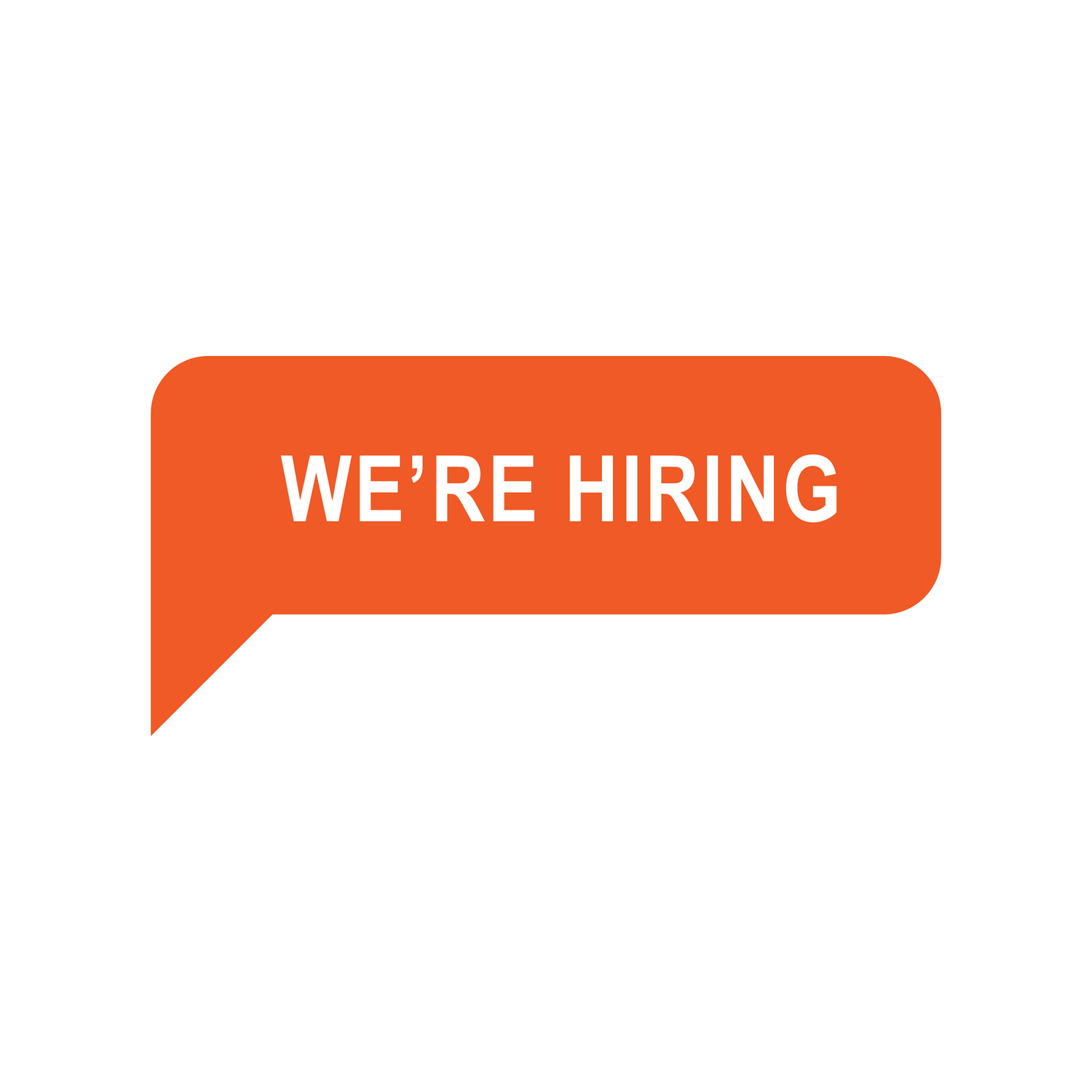
NextEra
2024-11-05 08:39:40
Dallas,
Texas,
United States
Job type: fulltime
Job industry: Mining / Oil / Gas
Job description
NextEra Energy Resources participates in pipeline infrastructure development, construction, management and operations through either wholly owned subsidiaries or joint ventures. We participate in 21 pipelines across 10 states to help provide access to domestic fuel sources, including clean-burning natural gas. Are you interested in being part of our best-in-class origination team
• Join our team today.
Position Specific Description
General Employee Responsibility:
The general responsibility of all employees is to work and act in a manner which contributes to the achievement of corporate, project, and individual goals.
The Plant Mechanic will have responsibility for performing maintenance and repair activities at McCommas which have been assigned to him/her. The Plant Mechanic will ensure that the following four priorities identified above are observed at all times:
1. Safety:
The Plant Mechanic will -
a. Work to maintain facility property and equipment in a safe condition such that the risk of fire, accident or injury is minimized.
b. Ensure that any and all activities conducted onsite by company personnel, contractors, or visitors are in keeping with the Safety and Health Policy Manual, NFPA Standards for Electrical Safety in the Workplace, and OSHA regulations.
c. Follow all established safety policies and processes, including the use, documentation and participation in tailboard meetings prior to commencement of onsite work.
d. Wear and/or utilize Personal Protective Equipment (PPE) appropriate for the work being performed.
e. Conduct equipment, tooling, and safety equipment inspection as assigned. This may include, but is not limited to fire extinguishers, hoists, chains, ladders, hand and power tools, mobile equipment and vehicles, etc.
f. Report safety incidents - accidents, injuries, occupational illness, and near misses - through the proper channels as per the Safety and Health Policy Manual.
g. Participate in periodic safety reviews in conjunction with Plant Manager and other Safety management personnel, including certification in CPR, First Aid, OSHA Safety Training, NFPA 70E Standard for Electrical Safety in the Workplace, fire extinguishers, and hazardous materials
h. Work to ensure that facility is maintained in a clean, orderly, and safe condition at all times.
2. Compliance:
The Plant Mechanic will -
a. Work to ensure that the plant is maintained and repaired in accordance with the limits and requirements of all relevant permits and authorities having jurisdiction.
b. Participate in monitoring and recordkeeping activities as assigned for the purpose of compliance.
c. Adhere to environmental policies and processes, in particular the Spill Prevention, Control, and Countermeasure plan (SPCC).
d. Promptly report any incidents or conditions which may result in a potential non-compliance status of a plant or piece of equipment through the proper channels.
e. Participate in periodic compliance reviews in conjunction with the Plant Manager and/or the Environmental and Safety Manager(s).
3. Performance:
The Plant Mechanic will -
a. Ensure that the plant and all equipment are maintained in such a state that production is maximized, downtime is minimized, and production goals are consistently met or exceeded.
b. Alert the Plant Manager regarding any mechanical or operational issues which could result in potential significant deviation from performance targets.
Specific Duties and Responsibilities
A. Plant Maintenance
1. Be proactive - observe all aspects of facility performance, identify opportunities to improve performance, and communicate potential improvements to Plant Manager.
2. Plan and coordinate daily routine maintenance of the facility, outage maintenance, and facility project work in order to minimize downtime.
3. Conduct all work in a safe manner, observing all safety regulations and safety policies and procedures.
4. Be adept in the proper use of electrical and mechanical hand tools used to remove, install or repair mechanical or electrical equipment.
5. Work with the Plant Manager and Plant Engineer on project schedules, costs and milestones to ensure that the budget and schedule for planned maintenance events are completed well in advance and once underway, that deadlines are met.
6. Work in conjunction with the Plant Manager and Plant Engineer in coordinating and conducting annual Fall Outage work and major onsite work and/or projects, to ensure their safe and timely completion. Be the lead on work teams involved in major maintenance activities as assigned during annual Fall Outages.
7. Ability to install, repair, maintain and/or upgrade computer controlled or electronic mechanical systems.
8. Ability to read and interpret schematics, blueprints, wiring diagrams and P&IDs to properly install, configure and/or troubleshoot and repair existing equipment or systems.
9. Recognize and promptly report to the Plant Manager any and all deviations from normal operating status which may have the potential to be a non-compliance event.
10. Take the lead on the performance of routine maintenance on rotating equipment, pumps, and other equipment, and work in concert with the on-shift Plant Operator where needed in performing routine maintenance or repair.
11. Be adept at the operation of forklifts, manlifts, and the like.
12. Work cooperatively at all times with other Plant Operators, Wellfield personnel, and management to ensure the safe, efficient operation of the facility.
13. Promptly take appropriate actions in conjunction with the on-shift Plant Operator to adjust or restore operations as needed which occur as the result of equipment malfunction.
14. Take the lead, in conjunction with Plant Manager, to help manage onsite inventory of major components (i.e., pumps, electric motors, control valves, solenoids, etc.) to ensure that adequate materials, supplies, spare parts, tooling, etc. are either onsite or are promptly available.
15. Maintain through provided training the following certifications: CPR, First Aid, OSHA Safety Training, Fire Extinguishers, Hazardous Materials.
16. Conduct regular preventative maintenance activities as assigned in accordance with manufacturer's operation and maintenance guides and/or procedures.
17. Maintain detailed and accurate records in the logbook of equipment maintenance and repair, installation of new parts, filling of vessels or reservoirs, etc., including date and time of work and a detailed description of the work performed.
18. Recognize, analyze and diagnose equipment issues in conjunction with other personnel and/or outside contractors/service providers.
19. Regularly participate in facility cleaning and housekeeping work, maintaining all aspects of the Maintenance Shop in a safe and presentable condition, as well as the exterior of the facility (H2S systems, Oberlin Filter Press area, compressor skids, PSA and TSA areas, parking areas, etc.).
B. Miscellaneous Duties
1. Other activities and duties as directed by the Plant Manager or other management personnel.
Job Overview
Employees in this role perform advanced technical tasks in support of the engineering, information systems, environmental, plant water chemistry, maintenance planning, cooling pond operation, procurement, inventory, statistical process control, production assurance, Land administration, and document control functions to support the plant mission.
Job Duties & Responsibilities
• Performs advanced supplier contract coordination functions and technical tasks with minimal direction to support the plant mission
• Develops and implements procedures that ensure safe, reliable, and cost effective operations
• Plans, schedules, and executes project activities
• Applies knowledge of permits and regulations to assist in taking appropriate action to prevent exceedances
• Performs other job-related duties as assigned
Required Qualifications
• High School Grad / GED
• Experience:3+ years
Preferred Qualifications
• Associate's Degree
NextEra Energy offers a wide range of benefits to support our employees and their eligible family members. Click here to learn more.
Employee Group: Non Exempt
Employee Type: Full Time
Job Category: Technicians
Organization: NextEra Energy Pipeline Services, LLC
Relocation Provided: Yes, if applicable
NextEra Energy is an Equal Opportunity Employer. Qualified applicants are considered for employment without regard to race, color, age, national origin, religion, marital status, sex, sexual orientation, gender identity, gender expression, genetics, disability, protected veteran status or any other basis prohibited by law. We are committed to a diverse and inclusive workplace.
NextEra Energy provides reasonable accommodation in its application and selection process for qualified individuals, including accommodations related to compliance with conditional job offer requirements, consistent with federal, state, and local laws. Supporting medical or religious documentation will be required where applicable and permitted by applicable law.
NextEra Energy will not discharge or in any other manner discriminate against employees or applicants because they have inquired about, discussed . click apply for full job details