Please scroll down, To apply
EHS Manager - Direct Hire - Leading Manufacturer
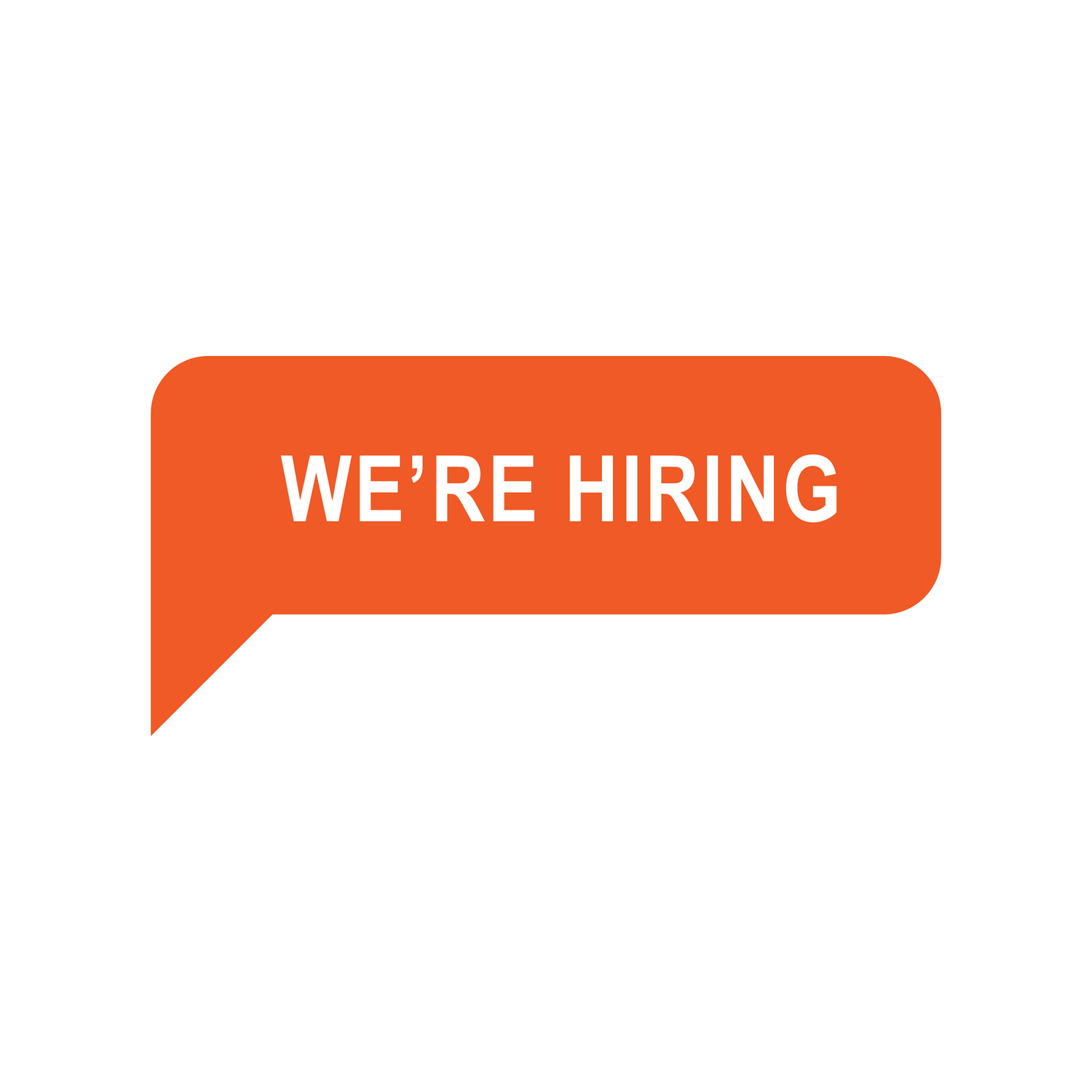
Manpower Engineering
2024-10-03 23:44:17
Madison,
Wisconsin,
United States
Job type: fulltime
Job industry: Engineering
Job description
EHS Manager - Direct Hire - Leading Manufacturer
Are you a passionate health and safety professional looking to make a significant impact?
We're partnering with a leading manufacturer to find a passionate EHS Manager to join their dynamic team. In this critical role, you'll play a key part in ensuring a safe, healthy, and environmentally responsible workplace.
What the position and company offer:
- Opportunity to make a real impact : Drive positive change in a company committed to safety excellence.This is an opportunity to make a real difference in a company that prioritizes safety and sustainability.
- Work for a growing, reputable company : Long and strong track record of success - 100+ years. Grown 27%+ in the past two years. The markets they serve are rapidly growing.
- High Visibility : You'll play a pivotal role in driving safety initiatives, ensuring regulatory compliance, and fostering a culture of safety excellence.
- Growth Opportunities: Great opportunity to develop technical expertise and leadership skills.
- Competitive Salary, Bonus, and Benefits
As the EHS Manager, you will be responsible for driving safety and environmental compliance across the company. Success in this role will be defined by your ability to develop and implement proactive, results-oriented health and safety initiatives, ensuring regulatory compliance while creating a culture of safety and continuous improvement.
Key Performance Objectives (KPOs):
- Develop and Implement a Comprehensive EHS Program
- Within the first 90 days, conduct a thorough audit of current safety and environmental practices, policies, and systems across all company sites. Identify gaps and opportunities for improvement.
- Create a strategic roadmap for achieving full compliance with OSHA, EPA, and other applicable regulatory bodies within 6 months.
- Gain buy-in from leadership and employees at all levels by presenting the roadmap and initiating company-wide rollout by the end of Q2.
- Achieve Zero Non-Compliance Incidents
- Over the first 12 months, ensure zero major non-compliance incidents with local, state, and federal regulations by driving continuous adherence to safety and environmental standards.
- Regularly audit compliance across all departments, ensuring corrective action plans are in place for potential non-conformance
- Reduce Workplace Incidents by 20% within the First Year
- By the end of year one, proactively reduce recordable workplace incidents by 20% through enhanced training, robust reporting mechanisms, and preventive measures
- Establish a data-driven safety reporting system that tracks leading and lagging indicators and use the data to adjust training and preventive strategies as necessary
- Present quarterly safety performance reports to leadership.
- Root Cause Analysis and Corrective Action
- Investigate all safety-related incidents (including near-misses) within 48 hours, identifying root causes and implementing corrective actions within 7 days.
- Create a formal process for conducting root cause analysis and trend tracking, ensuring continuous improvement in safety protocols
- Track and report on the effectiveness of corrective actions, providing insights to improve future processes.
- Lead Cross-Functional Safety Initiatives
- Within the first 6 months, establish and lead a cross-functional safety committee that meets monthly to address safety concerns, share best practices, and drive a company-wide culture of safety.
- Ensure all meetings result in actionable outcomes, with follow-up tasks assigned and tracked for completion
- Develop and Execute Company-Wide EHS Training
- Within the first 3 months, assess the current safety training programs and identify key gaps.
- Develop and roll out new and/or enhanced EHS training programs, ensuring 100% employee participation in mandatory sessions within the first 6 months.
- Ensure ongoing safety and environmental training are integrated into new hire onboarding and regularly update existing employees on emerging regulations and best practices.
- Improve Safety Data Analytics and Reporting
- Within 6 months, design and implement a robust safety data analytics platform to collect, analyze, and report on safety-related incidents, audits, and inspections.
- Provide monthly reports to leadership, identifying trends, high-risk areas, and suggesting solutions for ongoing improvement.
- Foster a Culture of Safety Awareness
- By the end of the first year, foster a proactive culture where safety is embedded in everyday practices at all levels of the organization.
- Introduce incentive programs or recognition systems to encourage employee participation in safety improvement efforts.
- Conduct quarterly town halls or safety days to engage employees and reinforce the importance of safety across the organization .
- Within the first 12 months, maintain all safety-related records, inspection files, and databases, ensuring compliance and readiness for audits at any time.
- Act as the company's primary point of contact for all regulatory inspections, audits, and correspondence, ensuring that the company is well-prepared and maintains positive relationships with regulatory bodies.
- Reduction in safety incidents, accidents, and environmental violations.
- Measurable improvements in regulatory compliance and adherence to company policies.
- Increased employee engagement and participation in EHS programs.
- Bachelor of Science Degree in Industrial or Occupational Safety or equivalent is strongly preferred.
- Minimum of 3 years of manufacturing experience (hands-on) in the Health and Safety field (construction, industrial, heavy manufacturing industry preferred).
- Effective written and verbal communication skills.
- Self-starter who is passionate about safety and can lead the way.
- Able to motivate and maintain a sense of urgency to continuously improve safety performance.
- Proven experience facilitating problem solving tools and techniques.
- Passion and enthusiasm for the Safety profession - we want someone who is excited about the field and who stays current.
- Leadership skills, vision - we want someone who can inspire others and gain buy-in - a change agent for continuous improvement.
- Problem solving skills - both process and people - be able to give specific examples that demonstrate these skills.
- Either hands-on experience with OSHA regulations or proven experience in knowing where/how to get current info quickly and interpret correctly .
ManpowerGroup (NYSE: MAN), the leading global workforce solutions company, helps organizations transform in a fast-changing world of work by sourcing, assessing, developing, and managing the talent that enables them to win. We develop innovative solutions for hundreds of thousands of organizations every year, providing them with skilled talent while finding meaningful, sustainable employment for millions of people across a wide range of industries and skills. Our expert family of brands - Manpower Engineering, Experis, Talent Solutions, and Jefferson Wells - creates substantial value for candidates and clients across more than 75 countries and territories and has done so for over 70 years. We are recognized consistently for our diversity - as a best place to work for Women, Inclusion, Equality and Disability and in 2022 ManpowerGroup was named one of the World's Most Ethical Companies for the 13th year - all confirming our position as the brand of choice for in-demand talent.
<!– job description page –>