Sr. Materials Manager - The Toro Company
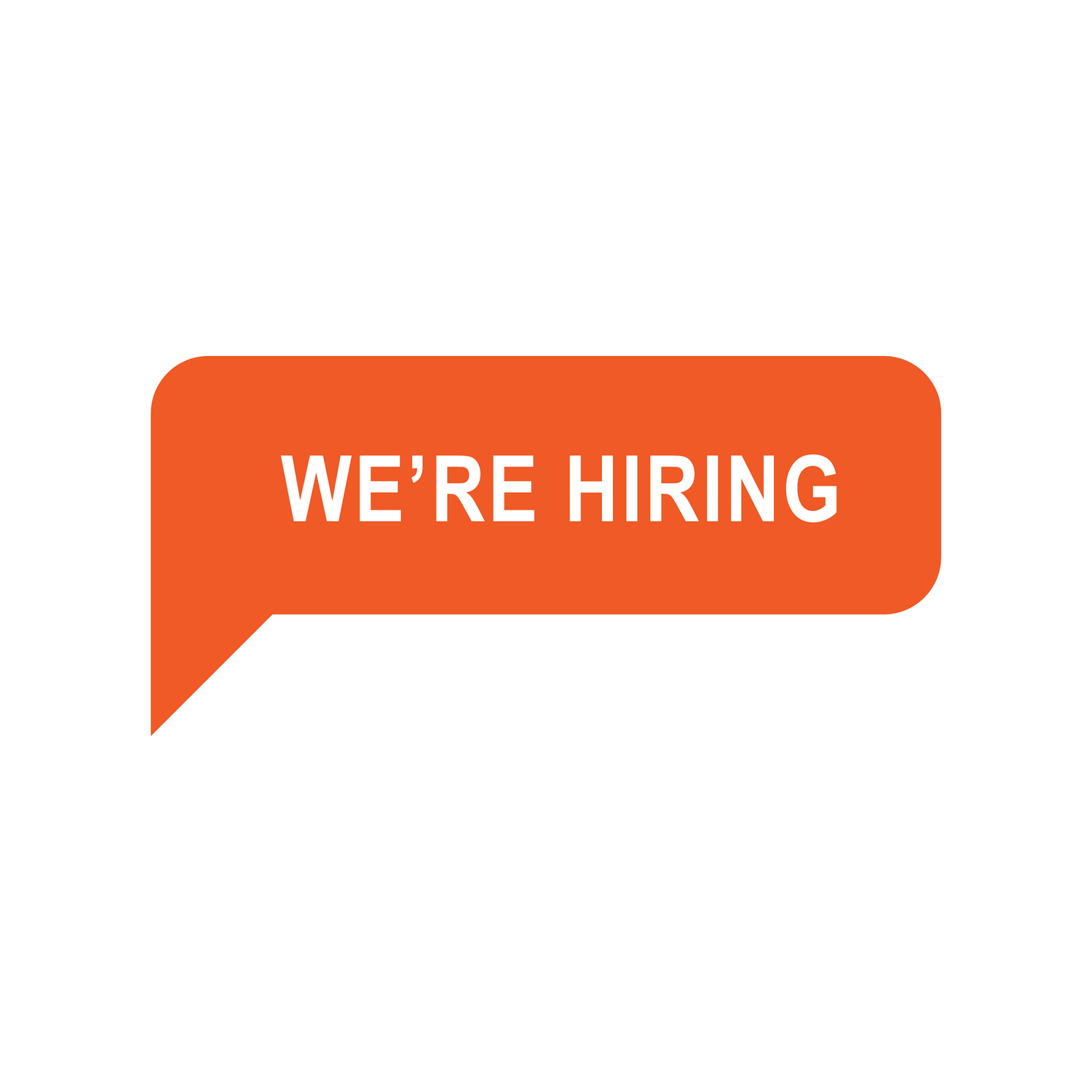
The Toro Company
2024-09-23 19:44:14
Tomah,
Wisconsin,
United States
Job type: fulltime
Job industry: Manufacturing Operations
Job description
Who Are We?
The Toro Company in Tomah, Wisconsin prides themselves on being a place for people to grow. The plant in Tomah stands out because it's a place that puts an emphasis on quality. Everyone at our facilities in Tomah knows that their step in the process is contributing to the finished product for the customer. All our locations build the intricate network of machinery that contributes to The Toro Company. We contribute to building communities, cities, and the world.
We invite you to apply and join a team of highly skilled, and highly passionate people.
Major Function:
This role reports to the Director of Operations and establishes the long-term materials planning strategy for the assigned site and optimizes daily execution levels to achieve ideal supply continuity. This position drives best practices across the Materials organization. Functional areas supported by this leadership position include planning, scheduling, production control, inventory management, warehouse operations, shipping, receiving and overall material flow throughout the site.
This position collaborates with other members of the plant leadership team to identify and address materials related issues and lead the supply planning process as part of the Integrated Business Planning system, which includes collaboration and alignment with other business and functional leaders.
What Will You Do?
In order to grow and build a successful career with The Toro Company, you will be responsible for :
- Drive SAP system design, deployment, and operational competency
- Develop robust Integrated Business Planning and SIOP process
- Manage capacity versus load to optimize utilization of plant capabilities and manufacturing efficiency
- Support lean systems implementation to include PFEP, Kanban, Pull, warehouse and market design, and material delivery loops delivering best practice resource deployment in Materials
- Research, recommend, and implement advanced technology to drive productivity in materials systems to include automated storage/retrieval, picking/put-away efficiency, mobile computing advancements, and advanced material handling solutions
- Drive continuous improvement in working capital measurements through inventory management initiatives that drive out waste, minimize excess/obsolete, complement lead time reduction, and improve overall turns
- Implement and scale up best practices to deliver on-going materials productivity
- Provide advanced materials analytics to guide local site leadership to areas of opportunity and synergy
- Ensure the Planners have all models scheduled in an efficient, logical manner to optimize site capacity and to accurately reflect the schedule in SAP
- Ensure all needed materials to support Master Schedules are planned, expedited, stored, and distributed in the most cost-effective manner
- Drive major performance goals including schedule attainment, work in process levels (WIP), finished goods level, service fill rates, inventory turns, inventory accuracy and budget controls
- Ensures service parts are, scheduled, produced and shipped per the required due date to maintain a 95% or higher fill rate
What Do You Need?
To be considered for this role, an individual should meet the following minimal requirements:
- Bachelor's degree (BA, BS) in Engineering, Manufacturing, Supply Chain, Business or similar field, or 10+ years of demonstrated accomplishment in achieving Materials and Manufacturing excellence
- Minimum of 5-7 years' experience in Material Requirement Planning Systems or a minimum of ten years combined experience of at least two of the following areas: Production Scheduling, Production Control, Inventory Control, Material Expediting or Warehouse Management.
- Strong organizational, interpersonal and team building skills. Must have direct supervisory experience.
- Strong management, communication, and leadership skills. Should be motivated with a positive attitude, with ability to work in a group/team setting
- Progressive experience in manufacturing environment demonstrating growth in position and/or responsibility
- Experience implementing various material signaling concepts such as kanban, min/max, ROP, MRP
- Proven experience implementing Lean material flow concepts, systems and tools such as Plan for Every Part (PFEP), pull systems, supermarkets, scheduling boards, Tugger routes, etc.
- Strong analytical skills with the demonstrated ability to analyze multifaceted, complex situations, problems, and concepts
- Strong written and verbal communication skills and the ability to effectively interact with individuals from a wide range of backgrounds
- Highly self-motivated and directed, able to work well under pressure, manage and prioritize multiple initiatives concurrently, attend to details, and meet deadlines
- Strong organizational skills, including the ability to be flexible, adaptable, and change priorities and direction as needed, allowing for optimum effectiveness
- Ability to coach and mentor others
- Aptitude and desire to gain understanding of situations, processes, and procedures in an effort to improve them
- Participate in organizational planning by participating in divisional conferences which include Quality, Design and Manufacturing Engineers, Plant Managers, Suppliers, and Purchasing. Liaison with suppliers concerning their manufacturing processes, quality systems, material schedules or rejected components
- Manufacturing setting with moving equipment and varying lighting, temperature and noise levels
- Typical office environment as it pertains to lighting, temperature, and noise level when in administrative/operations offices.
- Ability to work up to 100% of time in a manufacturing environment to collaborate with teams and identify/implement improvements
At The Toro Company, we are committed to fostering a secure and trustworthy recruitment process for our applicants. Recruitment fraud is a potential threat to job seekers, so please be aware that throughout our recruitment process, you'll never be required to pay any fees or disclose personal financial details when applying to TTC opportunities.
W e are proud to be an Equal Opportunity Employer and consider qualified applicants without regard to race, color, religion, sex (including pregnancy, gender identity, and sexual orientation), parental status, national origin, age, disability, genetic information (including family medical history), political affiliation, military service, or other non-merit based factors. We celebrate diversity and are committed to creating an inclusive environment for all employees.