Maintenance Manager
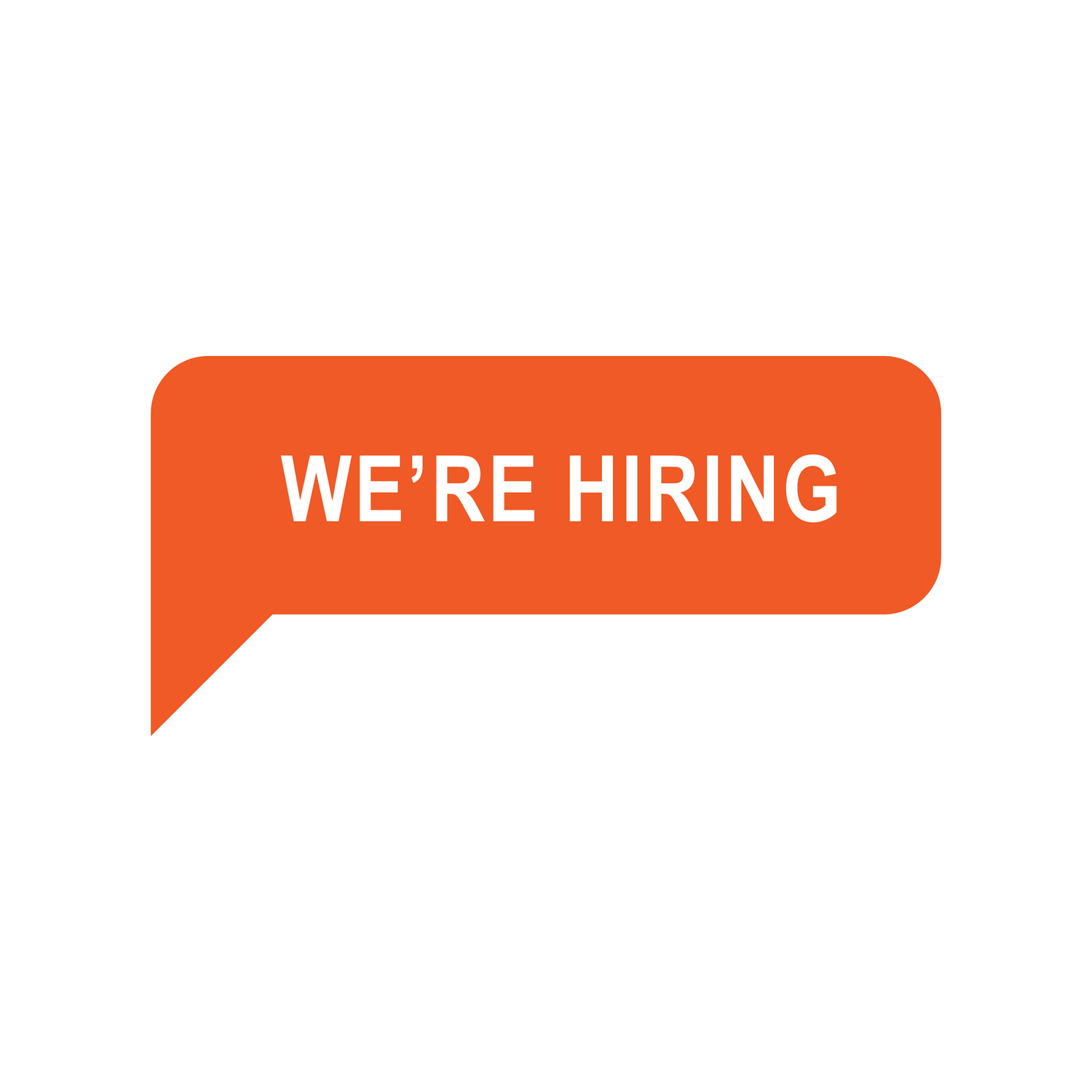
GoMacro LLC
2024-11-05 05:42:54
Viola,
Wisconsin,
United States
Job type: fulltime
Job industry: Executive Positions
Job description
Description:
Why join the GoMacro team?
We're a company that is driven by a unique core ideology we call The GoMacro Way, which is based upon authenticity, generosity, and compassion for people and the planet. We operate with integrity, we create with passion, and we conduct ourselves with humility. We seek growth-minded people who are inspired by challenges, encouraged by camaraderie, and excited about being leaders at every level. Become part of a team where everyone is heard, valued, and empowered to influence positive change in their local and global community.
How GoMacro's history shapes who we are today?
During her 2003 battle with cancer, co-founder Amelia Kirchoff created the first MacroBar recipe in her kitchen on the Wisconsin family farm. In the years following, Amelia and her daughter and co-founder Jola began spreading awareness for the power of a balanced, plant-based lifestyle through GoMacro's healthy and delicious MacroBars, which are now available in stores nationwide.
Today, our work is still guided by the values upon which Jola and Amelia built GoMacro: Live Long, Eat Positive, Give Back, Tread Lightly, and Be Well. It's our goal to inspire people to have a healthy body, sharp mind, and bold spirit-and we believe doing fun, and meaningful work is part of that.
Join us as we make the world better, one bite at a time!
Position Description:
The Maintenance Manager will provide leadership and hands-on direction to efficiently produce quality products in a high-performance team. The Maintenance Manager will enjoy a high-change environment and must be extremely adaptable to changing priorities.
The Maintenance Manager works collaboratively to mobilize and direct maintenance resources in maximizing production equipment performance to meet plant KPIs, including safety, food safety, productivity, and quality metrics. This role will drive a culture of accountability and provide extraordinary service to the Production team.
Candidates who connect through positive and respectful interaction, inspire greater success, and create extraordinary experiences, solutions and ideas will be at the top of our list.
Primary Responsibilities:
- Analyzes and solves technical maintenance issues.
- Encourages and monitors the development of maintenance technician skills - both technical and leadership.
- Ensures safe working conditions for associates and compliance with all state and federal regulations on environmental, health, and safety issues.
- Manages and develops plant maintenance programs to ensure minimal downtime.
- Directs employees engaged in facilities and grounds maintenance activities.
- Implements systems to ensure that products are manufactured in a safe, sanitary, and efficient manner.
- Identifies, implements, and manages capital improvement projects.
- Conducts performance appraisals of the Maintenance team and recommends and/or implements appropriate training programs to address developmental needs.
- Assures an effective PM program for the facility.
- Administers and audits all safety control programs and environmental protection programs.
- Develops training programs for maintenance supervision and mechanics.
- Develops short and long-term planning, objectives, programs and goals, and department budget and cost controls.
- Requisitions spare parts, tools, equipment, and supplies.
- Inspects completed work for conformity to blueprints, specifications, and other building standards.
- Trains, instructs employees, conducts performance reviews, initiates discipline, recommends transfers, or wage increases; maintains good employee relations
- Other job duties, responsibilities, and activities may change or be assigned at any time with or without notice
Skills Required:
To perform this job successfully, an individual must be able to perform each essential duty satisfactorily. The requirements listed below are representative of the knowledge, skill, and/or ability required. Reasonable accommodations may be made to enable individuals with disabilities to perform essential functions.
- Current knowledge of occupational health and safety (OSHA) standards, the Americans With Disabilities Act (ADA), and other applicable rules, regulations, and practices
- Knowledge of the proper operation and routine maintenance and repair of food manufacturing equipment and vehicles
- Knowledge of the proper use of tools and equipment used in facilities, equipment, and grounds maintenance
- Knowledge of and ability to operate hand and power tools
- May be required to operate motor vehicles and light trucks
Education/Training Required:
- High school diploma or general equivalency diploma (GED) with additional supervisory or management courses (an equivalent combination of education and experience may be substituted)
- Apprenticeship or its equivalent in a formal trade school education
- Three to five years of experience in Maintenance Leadership
Travel Required:
Travel will be primarily local during business hours.
Physical Demands:
The physical demands described here are representative of those that must be met by an employee to successfully perform the essential functions of this job. Reasonable accommodations may be made to enable individuals with disabilities to perform the essential functions.
While performing the duties of this job, the employee is frequently required to sit; talk or hear, and use hands to handle, or touch objects or controls. The employee is regularly required to stand and walk. On occasion, the incumbent may be required to climb, stoop, bend or reach above the shoulders. The employee must occasionally lift up to 50 pounds. Specific vision abilities required by this job include close vision, distance vision, color vision, peripheral vision, depth perception, and ability to adjust focus.
Work Environment:
Work is mainly performed in a normal office environment and occasionally completed outside in all weather conditions and on uneven terrain or in garage structures that are often cooler or hotter than normal offices. Noise levels are usually moderate (normal office) and occasionally high due to the use of the equipment and the running of vehicle engines.
The above statement reflects the general details necessary to describe the principal functions of the occupation and shall not be construed as a detailed description of all the work that may be inherent in the occupation.
PIa00226bc5-